¿Qué es moldeo por inyección?
El moldeo por inyección es un proceso de manufactura muy usado para producir partes plásticas en grandes volúmenes. Este proceso implica usar una máquina de moldeo por inyección para fundir el material, inyectarlo a un molde bajo presión y producir componentes de la forma deseada tras el enfriamiento.
Una gran parte de las partes plásticas en nuestro día a día son moldeadas por inyección. Estas partes incluyen artículos como cepillos dentales, partes de automóviles y armazones de aparatos de cocina.
Este tipo de moldeo es popular debido a su bajo costo unitario y su capacidad de fabricar formas complicadas con calidad constante. Los plásticos, principalmente los polímeros termoplásticos, se usan como la materia prima que puede ser coloreada o rellenada con aditivos.
Se requiere un alto grado de flexibilidad de diseño. En comparación con otros procesos de manufactura como la máquina de CNC (control numérico computarizado), el moldeo por inyección permite una significativamente mayor variedad de texturas y materiales de superficie.
Equipo de moldeo por inyección
En el aspecto técnico, el proceso de moldeo por inyección requiere una máquina de moldeo por inyección y un molde fabricado específicamente para la parte que se producirá.
Máquina de moldeo por inyección
Una máquina de moldeo por inyección se compone de tres partes principales: la unidad de inyección, el molde y la unidad de cierre o expulsión.
Dentro de la unidad de inyección, una tolva alimenta el plástico a un pistón en forma de tornillo y a la unidad de calentamiento. Una vez que se ha acumulado la cantidad de plástico líquido requerida, se inicia el proceso de inyección.
El material se funde mediante calor/corte y se inyecta a un molde con alta presión. Ahí, se forman las partes moldeadas por inyección.
La unidad de cierre o unidad de expulsión tiene la tarea de abrir y cerrar el molde y expulsar los productos moldeados. Las unidades de cierre con rodillera son las más comunes y consisten en platinas para sostener el molde. Estas platinas, por lo general acomodadas de forma vertical en el marco de la máquina de moldeo por inyección, pueden compararse con una prensa interna que ejerce una fuerte presión de cierre. De manera alternativa, las unidades de cierre tipo hidráulico usan un cilindro hidráulico para ejercer la fuerza de cierre en el molde.
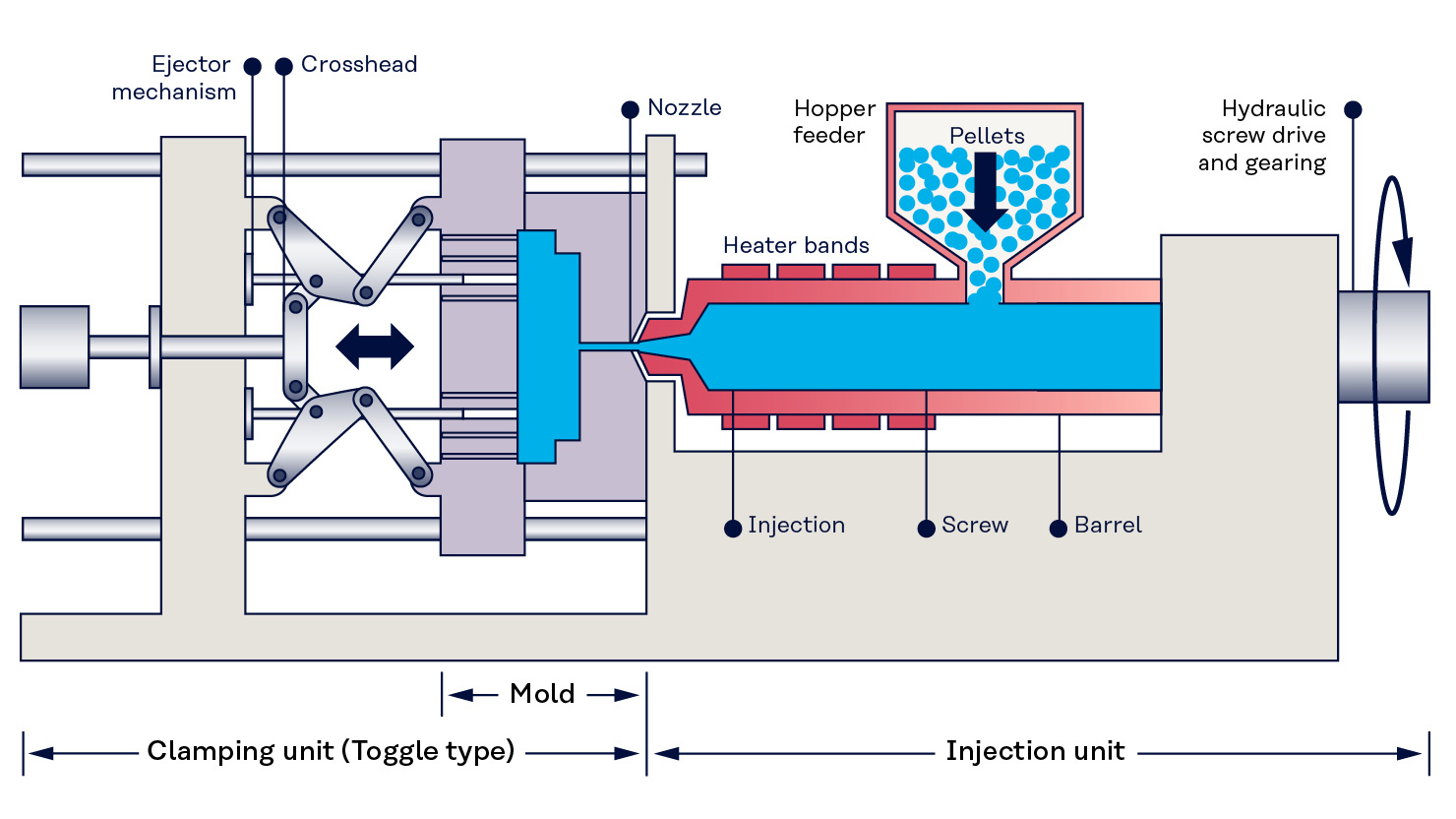
Fuerza de cierre
La fuerza de cierre puede variar de algunas toneladas a varios miles de toneladas. Debido a este amplio rango, las prensas comúnmente se clasifican por su tonelaje, el cual indica la fuerza de cierre que la máquina puede ejercer. El tonelaje requerido para moldear una parte específica depende de su área proyectada.
La regla de oro es normalmente 5 toneladas por pulgada cuadrada para la mayoría de los productos; sin embargo, se aplican algunas excepciones para materiales plásticos muy rígidos, ya que requieren una mayor presión de inyección y fuerza de cierre para mantener el molde cerrado. Las partes más grandes también requieren una mayor fuerza de cierre.
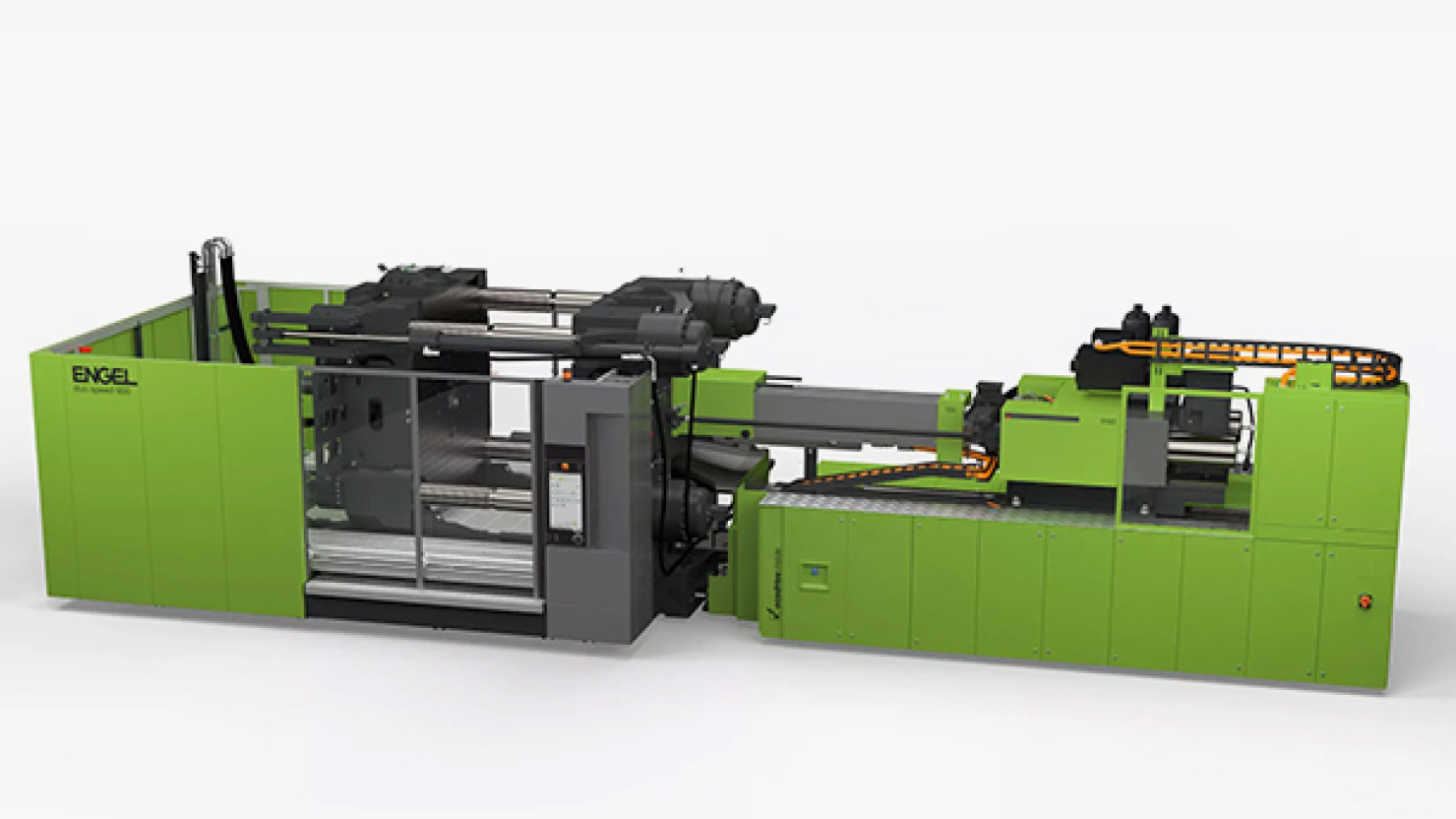
Molde
El molde, en ocasiones referido simplemente como una “herramienta”, es el corazón del proceso completo. Es un bloque metálico hueco en el que se inyecta el plástico líquido para crear la forma deseada. El molde tiene varios orificios para el control de temperatura y ventilación. La temperatura se controla usando agua, aceite o un calentador.
En su forma más simple, el molde consiste en dos mitades:
- La cavidad (el frente) y
- el núcleo (el reverso).
Por el contrario, las partes moldeadas por inyección por lo general cuentan con dos lados:
- El lado A de una parte, por lo general la parte visualmente más llamativa, mira hacia la cavidad.
- El lado B, también llamado lado funcional, por lo general contiene los elementos estructurales escondidos de la parte. Su superficie es, por lo tanto, rugosa y muestra rastros de los pines o sujetadores del expulsor.
El plástico líquido fluye mediante un canal de colada hacia el molde y llena sus cavidades. Tras el enfriamiento y la solidificación, que por lo general representa cerca de la mitad del ciclo de moldeo por inyección, el molde se abre y las partes moldeadas son expulsadas.
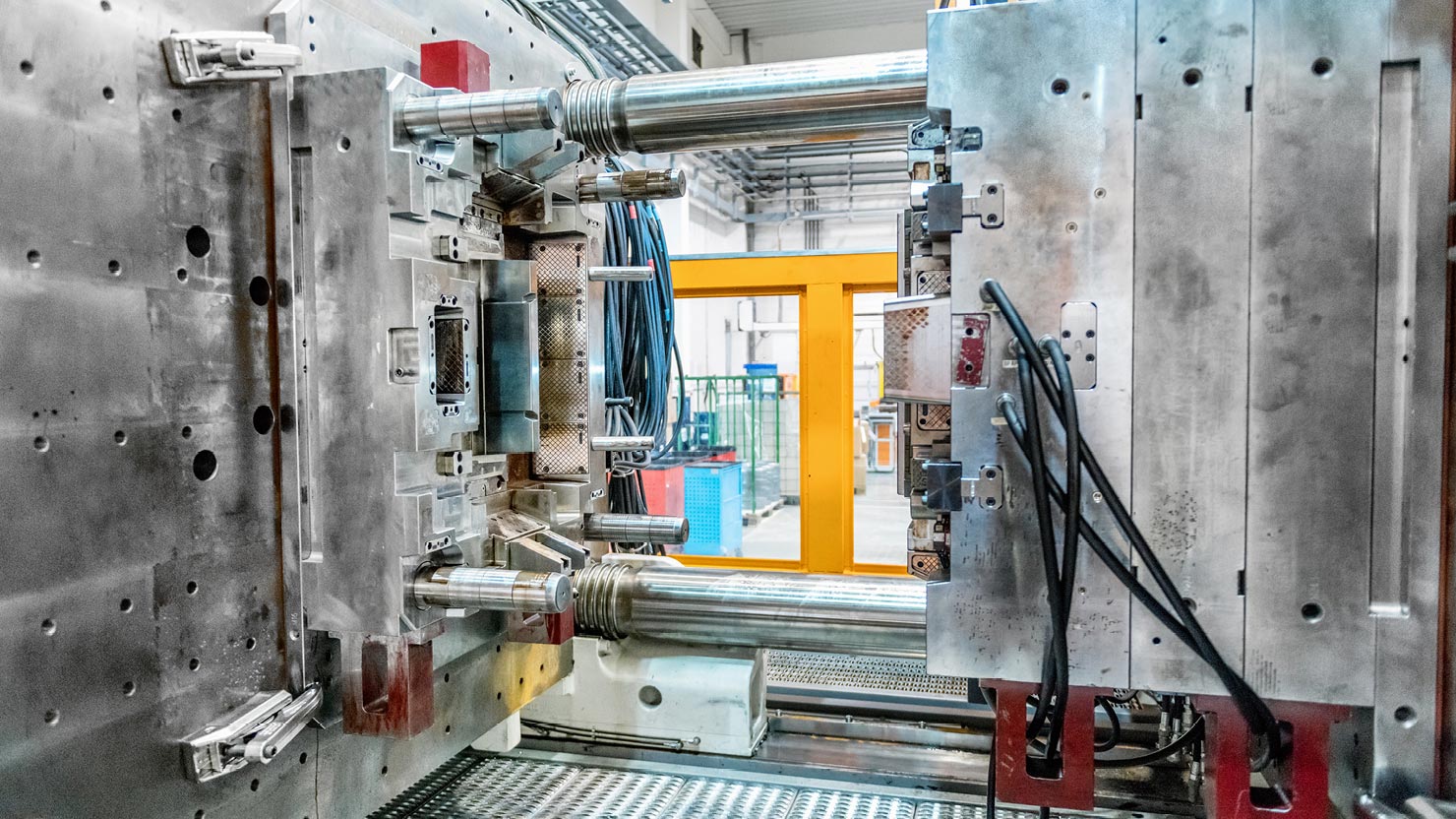
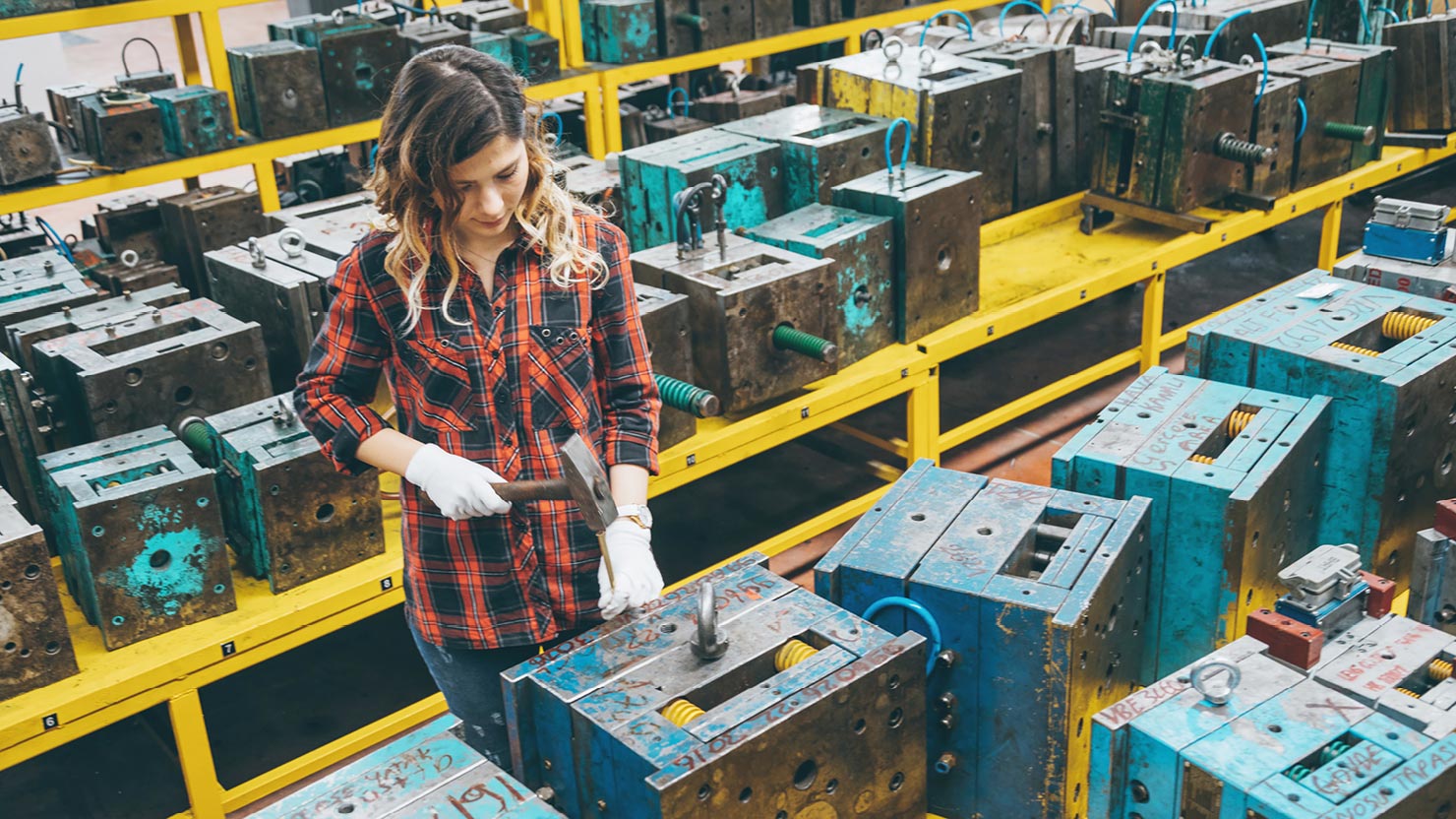
Datos útiles
Los moldes son costosos de fabricar y, por este motivo, se usan para la producción masiva de miles hasta millones de partes. Por lo general se fabrican de acero endurecido o pre-endurecido, pero también se pueden hacer de aluminio y/o una aleación de cobre de berilio.
Material del molde
Los moldes de acero son más caros de producir, pero también duran más. Si se puede producir un mayor número de partes, el costo del molde de acero entonces justifica el costo añadido. Los moldes de acero endurecido son superiores en resistencia al desgaste y durabilidad. Los moldes de acero pre-endurecido son menos resistentes al desgaste y se utilizan para cantidades menores o partes mayores.
Los moldes de aluminio menos costosos pueden ser económicos para la manufactura de decenas o incluso centenas de miles de partes. La aleación de cobre de berilio se usa cuando se requiere una disipación rápida de calor o cuando existe un grado alto de calor de corte.
Diseño de molde
El molde puede compararse con un negativo de una fotografía, donde la estructura superficial y la geometría del molde se transfiere a la parte terminada. También incluye características como el sistema de compuertas para dar lugar al flujo del material y canales internos de enfriamiento.
A fin de producir miles o incluso millones de partes con precisión y repetibilidad, los fabricantes de moldes requieren de gran experiencia y conocimiento. Esto se debe a que un molde puede ser muy complejo con varias consideraciones como el grosor de la pared, esquinas, nervaduras, rebajes y roscas. El gran esfuerzo de desarrollo es otra razón por la que el molde por lo general representa la mayor parte de los costos de arranque en el moldeo por inyección.
El costo de los moldes puede variar en gran medida: los moldes de trazado rectocon geometrías muy simples para pequeñas corridas de producción son relativamente más fáciles de desarrollar y cuestan unos cuantos miles de dólares. Los moldes más avanzados para producción a gran escala y con geometrías complejas representan un costo mucho mayor, ya que requieren núcleos o insertos retractables. Estos elementos móviles se insertan en el molde desde arriba o abajo para producir partes con un elemento que cuelga, como una apertura o una cavidad.
El diseño del molde con frecuencia se hace de manera interna por los fabricantes de máquinas o empresas especializadas y requiere la consideración de materias primas y el uso de análisis de elementos finitos. Los fabricantes de moldes o de herramientas hacen moldes a partir de metales, por lo general acero o aluminio, y los fresan de manera precisa mediante CNC para formar las características deseadas. Avances recientes en materiales de impresión 3D permiten la producción de moldes para lotes más pequeños a un costo menor, en comparación con los métodos tradicionales.
El sistema de alimentación, también conocido como sistema de compuertas, controla el flujo y la presión y canaliza el plástico líquido hacia el molde. El plástico líquido fluye mediante los siguientes canales conforme entra al molde:
- El bebedero,
- canal principal,
- sub-canal y
- la compuerta o “puerto de alimentación”, que es un canal estrecho entre el sub-canal y la cavidad del molde
Asimismo, el pozo frío de residuos comúnmente recopila los residuos fríos en el proceso de moldeo por inyección para evitar el bloqueo en el sub-canal o compuerta, para que el material caliente restante pueda fluir hacia la cavidad del molde sin complicaciones.
La producción de múltiples partes con frecuencia requiere bebederos. Los sistemas de bebederos se separan de las partes tras la expulsión. El moldeo por inyección es un método de manufactura de baja generación de residuos, donde los sistemas de bebederos son el único residuo de material. Una parte de estos residuos pueden ser reciclados o reutilizados, dependiendo del material.
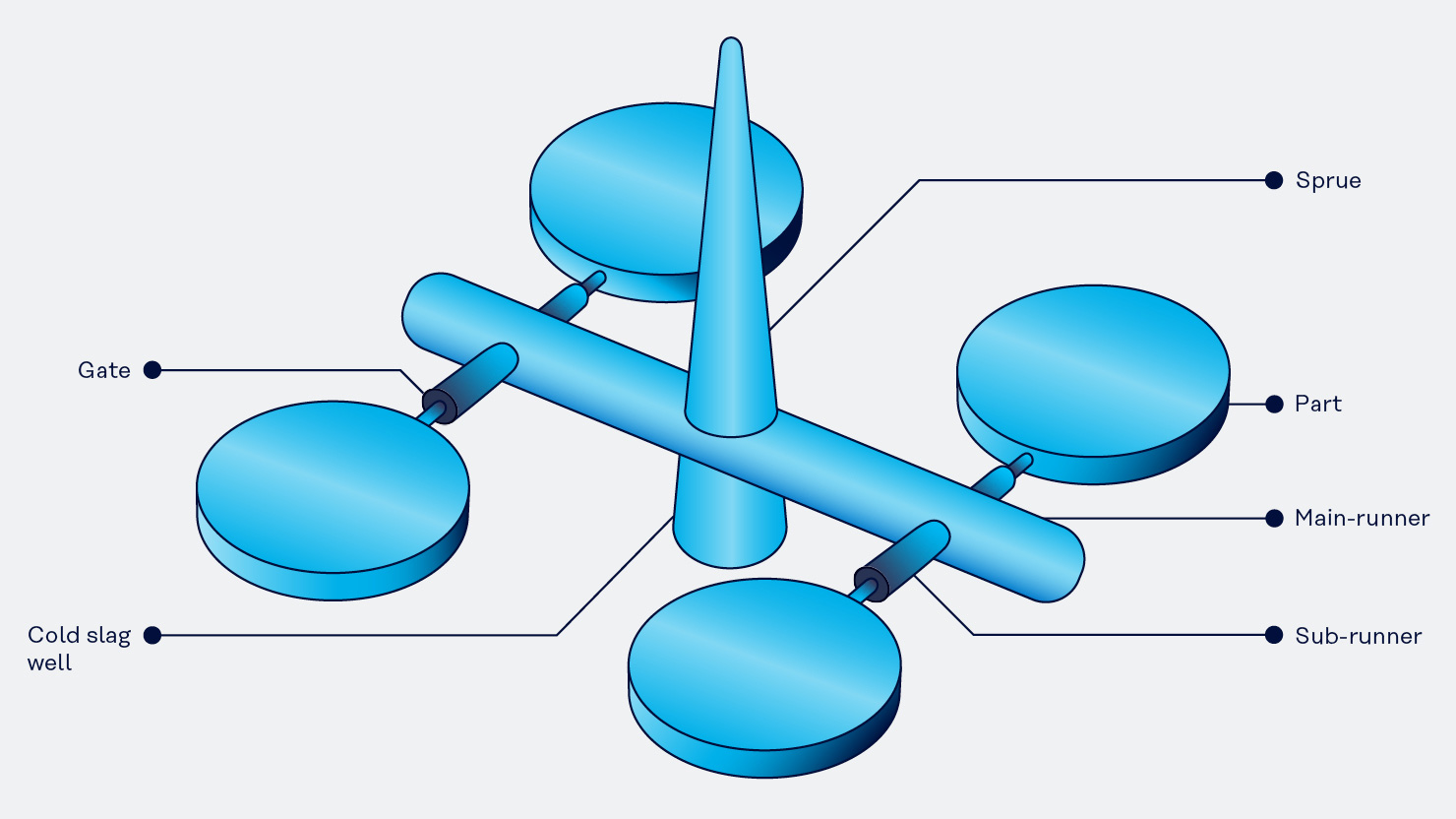
Los fabricantes de moldes pueden elegir entre varios tipos de compuertas dependiendo de diversos aspectos, como la orientación de la parte (lada A en comparación con lado B), facilidad de producción del molde, selección de material, flujo de material, tamaño de la parte, comportamiento de recortes y costo de los restos. Para obtener más información, consulte la guía de compuertas de moldeo por inyección de Basilius.
Los moldes también incluyen un sistema de cierre con dos fines principales:
- Mantener las dos partes del molde firmemente cerradas durante la inyección y
- empujar la parte moldeada por inyección fuera del molde tras la apertura.
La parte expulsada cae entonces sobre una cinta transportadora o un contenedor y se almacena o se ensambla.
Puesto que las diversas partes móviles del molde nunca pueden alinearse al 100%, es posible notar dos defectos en casi todas las partes moldeadas por inyección:
- Líneas divisorias, que son visibles cuando se encuentran dos mitades del molde y
- marcas del expulsor, causadas por los pines del expulsor.

Moldeo
El término “moldeo” hace referencia al material que llena el bebedero, el pozo frío de residuos, los canales, las compuertas y la sección de la cavidad del molde que forma las partes todas combinadas.
Dependiendo del material, el contenido del bebedero, el pozo frío de residuos, los canales y las compuertas pueden ser descartados -o remolidos y reutilizados en otro ciclo de moldeo por inyección.
Características del proceso
El ciclo del proceso para moldeo por inyección es muy corto y toma entre pocos segundos y dos minutos, dependiendo del tamaño de la parte. El proceso se puede dividir en cuatro pasos principales: cierre, inyección, enfriamiento y expulsión.
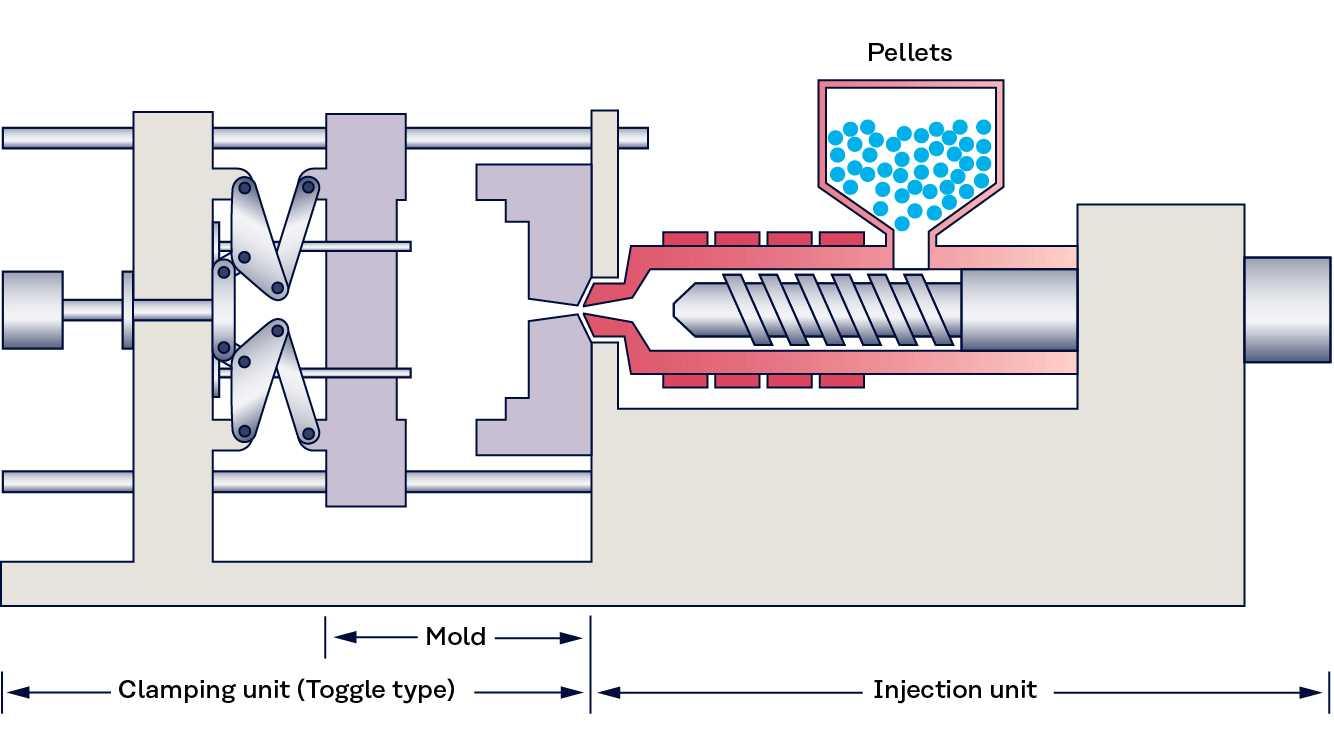
Paso 1: Cierre
Antes de la inyección del material al molde, las dos mitades del molde deben cerrarse de manera segura mediante la unidad de cierre. La unidad de cierra presiona las mitades del molde firmemente mientras que se inyecta el material. Las máquinas más grandes con mayores fuerzas de cierre requieren más tiempo para cerrar.
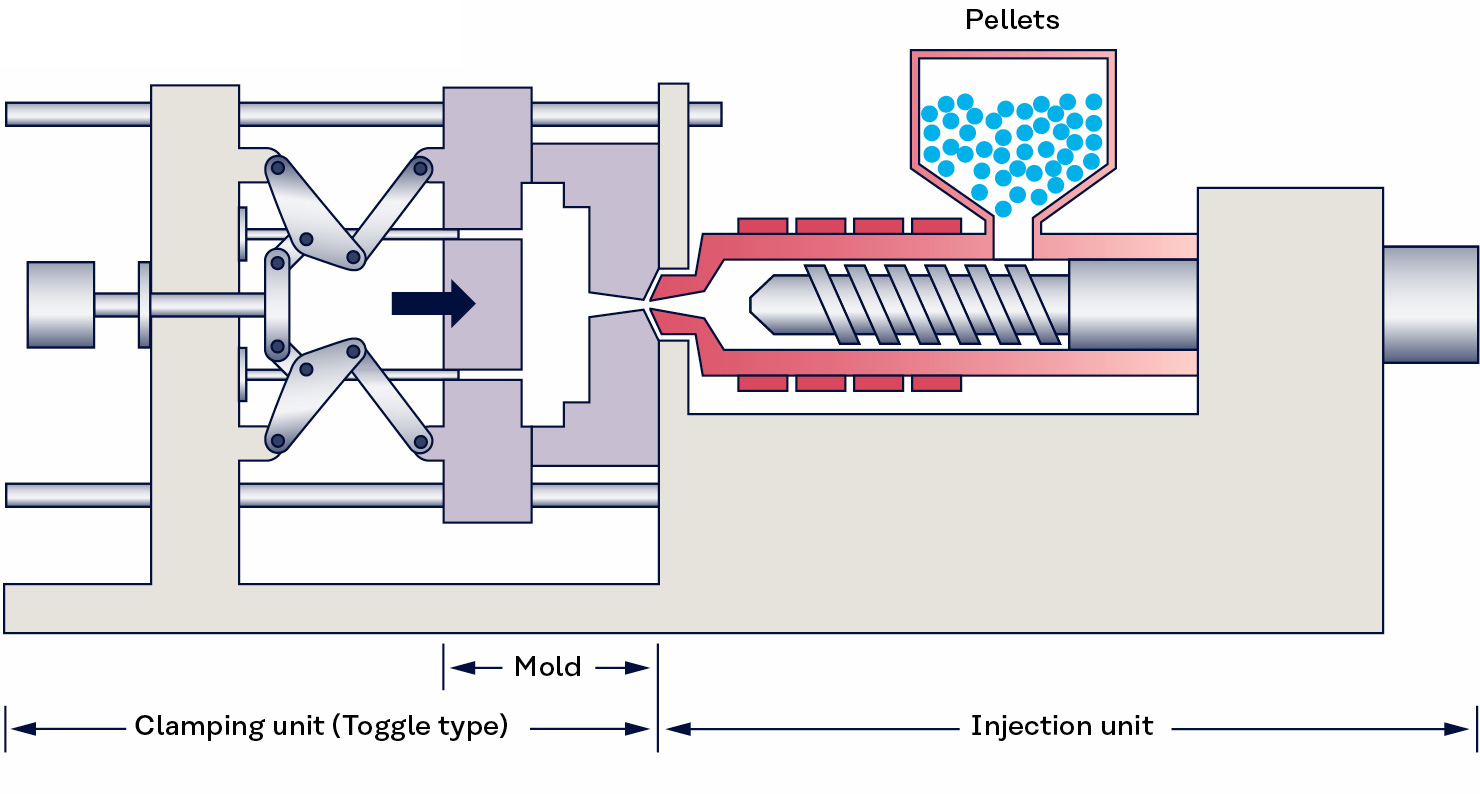
Paso 2: Inyección
La materia prima, por lo general gránulos de plástico, se transfiere de la unidad de inyección al molde, y así se funde mediante calor y presión. El plástico líquido, el disparo, se inyecta mediante el sistema de canal al molde, donde llena la cavidad completa.
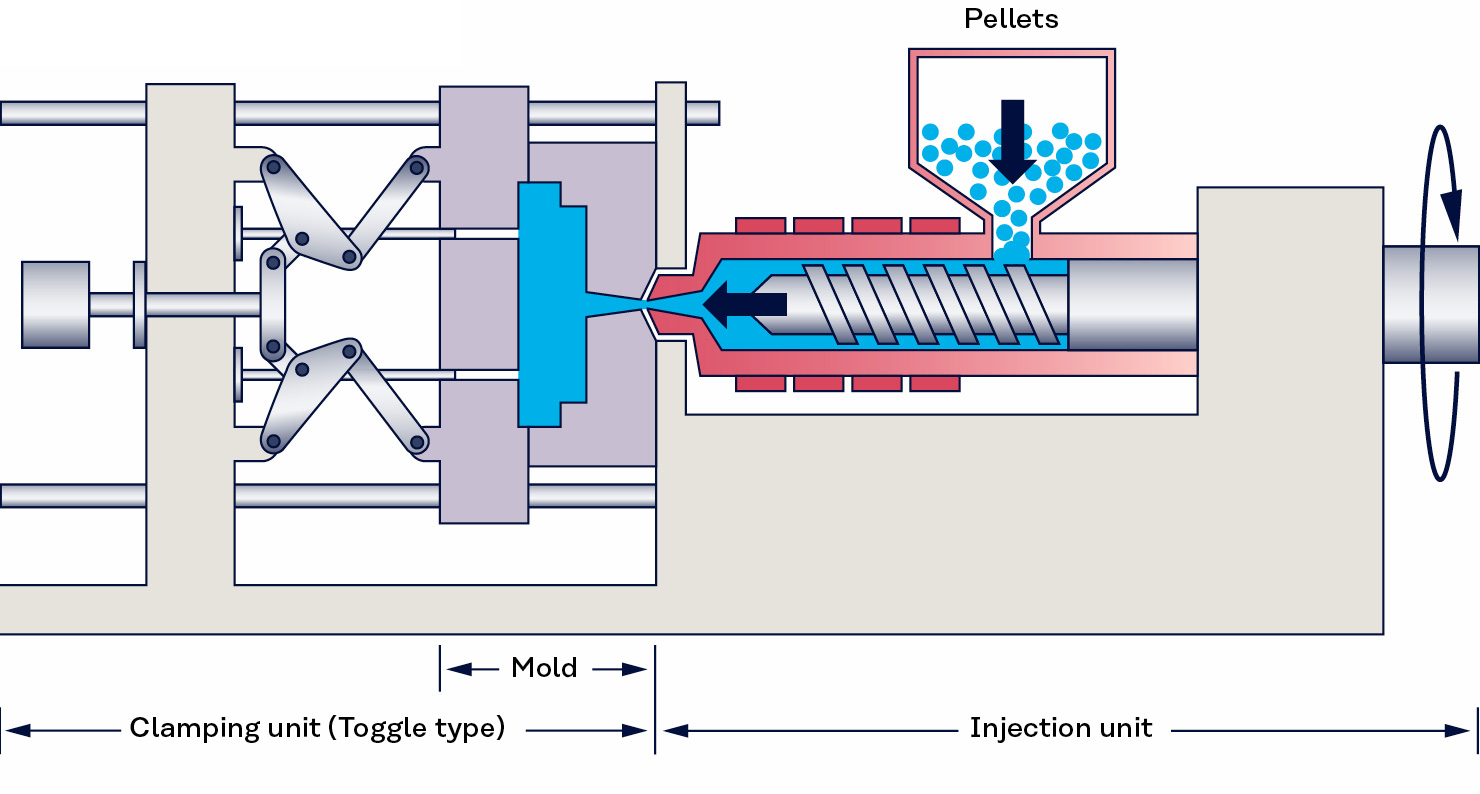
Paso 3: Enfriamiento
En el molde, el plástico líquido empieza a enfriarse en cuanto entra en contacto con las superficies internas del molde. Cuando el material se enfría, se solidifica de nuevo y toma forma. El molde permanece cerrado hasta que transcurra el tiempo de enfriamiento requerido.
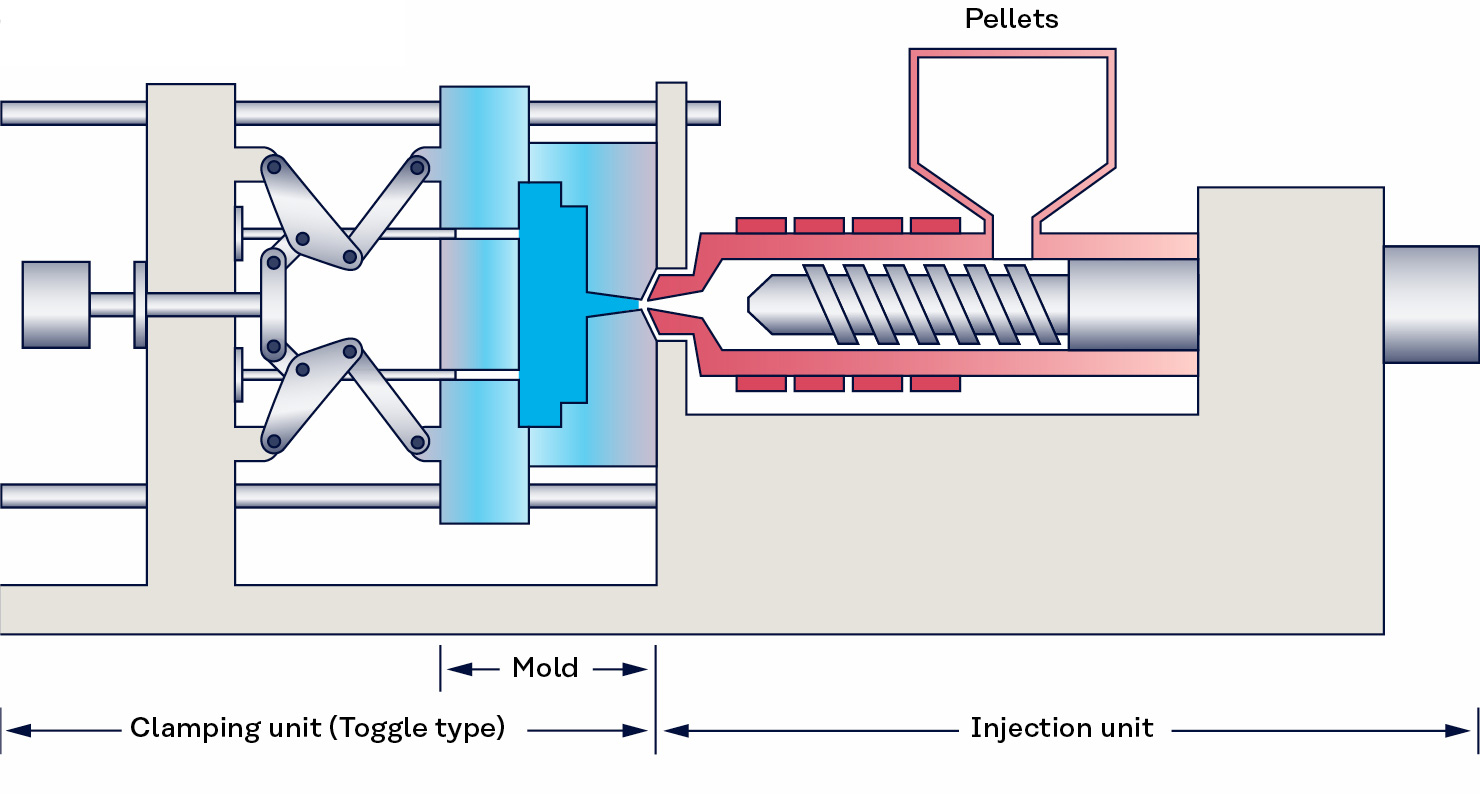
Step 4: Paso 4: Expulsión
La parte enfriada es expulsada del molde usando un sistema expulsor: cuando el molde se abre, la parte moldeada es expulsada del molde por un mecanismo. Dependiendo del diseño de la compuerta, la parte se separa automáticamente del resto del molde, o mediante corte.
Tras la expulsión, una cinta transportadora mueve la parte moldeada al almacenamiento, ensamblado o post-procesamiento. De manera simultánea, el molde se cierra de nuevo para el siguiente disparo y se repite el proceso de moldeo por inyección. En algunos casos, las partes moldeadas por inyección están listas para uso inmediato, mientras que otras requieren varios niveles de procesamiento posterior.
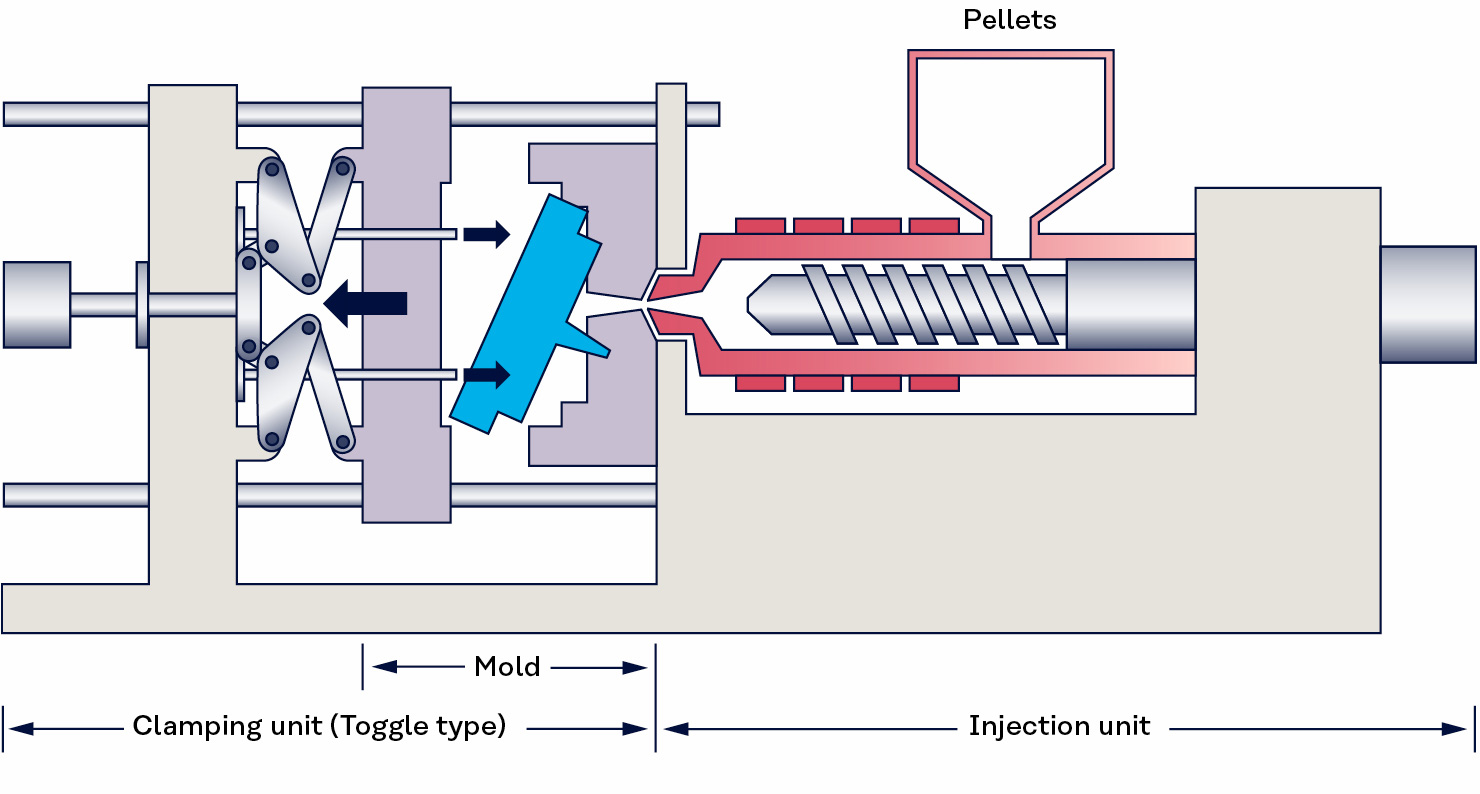
Tipos de moldeo por inyección
Moldeo por inyección tradicional versus moldeo por inyección disociada
En el moldeo por inyección tradicional, la inyección se realiza a una presión constante para llenar y comprimir la cavidad del molde; sin embargo, esto puede ocasionar que las dimensiones de los moldeos cambien en gran medida de un ciclo a otro.
En el moldeo por inyección disociada, el proceso de inyección se separa en dos etapas para lograr un mayor control de las dimensiones de las partes y consistencia en los disparos:
- Llenar la cavidad cerca de 98% usando un control de velocidad y después
- llenar el 2% restante usando control de presión.
El moldeo por inyección separado también se llama moldeo por inyección científico.
Moldeo por inyección de un componente y de múltiples componentes
En el moldeo por inyección de plásticos, se hace una distinción entre el moldeo por inyección de un componente y moldeo por inyección de múltiples componentes. Dependiendo del número de materiales utilizados, el moldeo por inyección de múltiples componentes se divide en moldeo por inyección 2K, moldeo por inyección 3K, etc.
2K se refiere al moldeo por inyección de dos componentes, donde un material suave (por ejemplo, TPE) se moldea alrededor de un material duro (por ejemplo, PP). 3K es similar a 2K, pero con una capa o componente adicional.
Posibles defectos
Es posible que ocurran varios defectos en el proceso de moldeo por inyección: defectos que dependen de la máquina o defectos que dependen del material, así como defectos que pueden depender de ambos, la máquina y el material.
La siguiente sección es un intento de clasificar los defectos y presentar ejemplos. En la práctica, hay tantas causas posibles de los defectos de partes moldeadas que sería ingenuo describirlos en un artículo escrito.
Defectos que dependen del equipo
Los defectos que dependen del equipo se deben a motivos técnicos. Por ejemplo, un excedente de material líquido puede escaparse del molde si la presión de inyección es muy alta o la fuerza de cierre del molde es muy baja, y a este defecto se le llama rebabas o flashing.
El enfriamiento disparejo puede ocasionar que algunas partes se deformen. Si el diseño del molde o el proceso de moldeado no considera de forma correcta el encogimiento que ocurre normalmente durante el enfriamiento, las partes se pueden deformar.
Aparecen burbujas en las partes moldeadas cuando el molde o el material está muy caliente. Este defecto por lo general está relacionado con la máquina y se genera por una falta de enfriamiento alrededor del molde o un calentador que no funciona como debería.
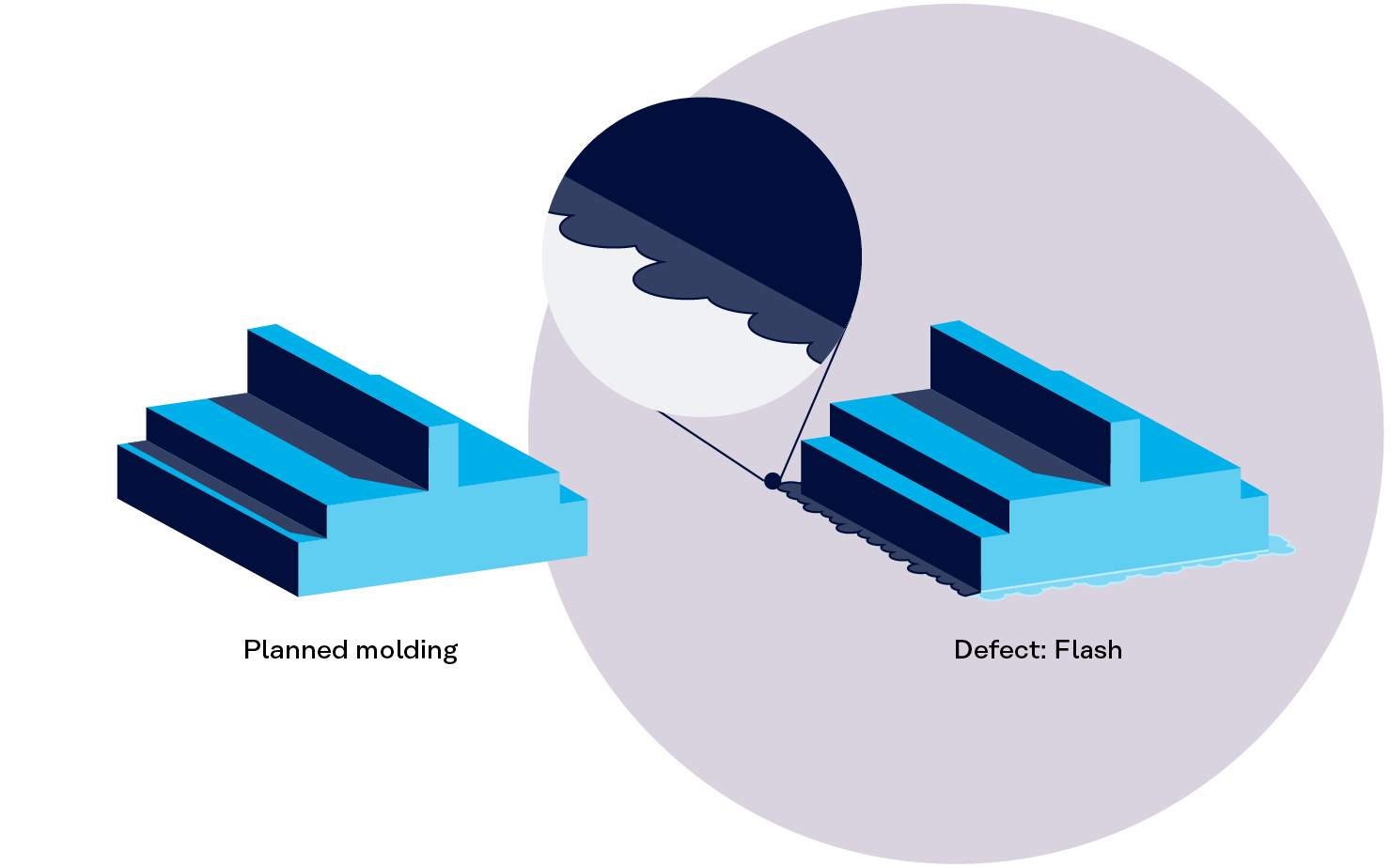
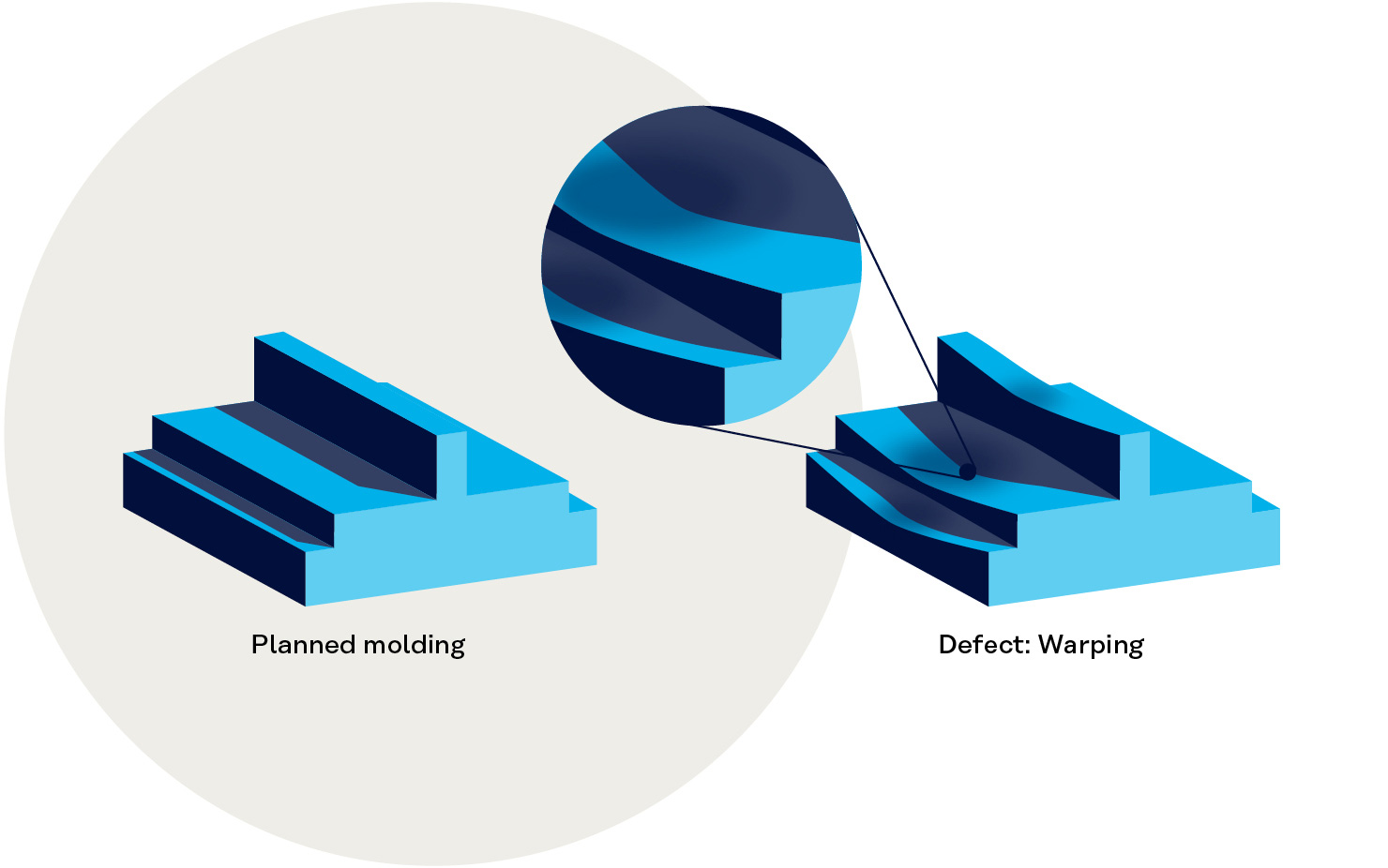
Defectos que dependen del material
La degradación de polímeros es un ejemplo de un defecto que depende del material. Si el material pasó por un proceso de hidrólisis, oxidación u otra causa de degradación de polímeros, las partes moldeadas lo mostrarán en forma de grietas, decoloración o defectos similares.
Otro defecto que depende del material: disparos cortos. Si no hay suficiente material en la máquina de moldeo por inyección, la parte moldeada tendrá secciones no rellenadas. De forma alternativa, esto puede ser la causa de una velocidad de flujo insuficiente.
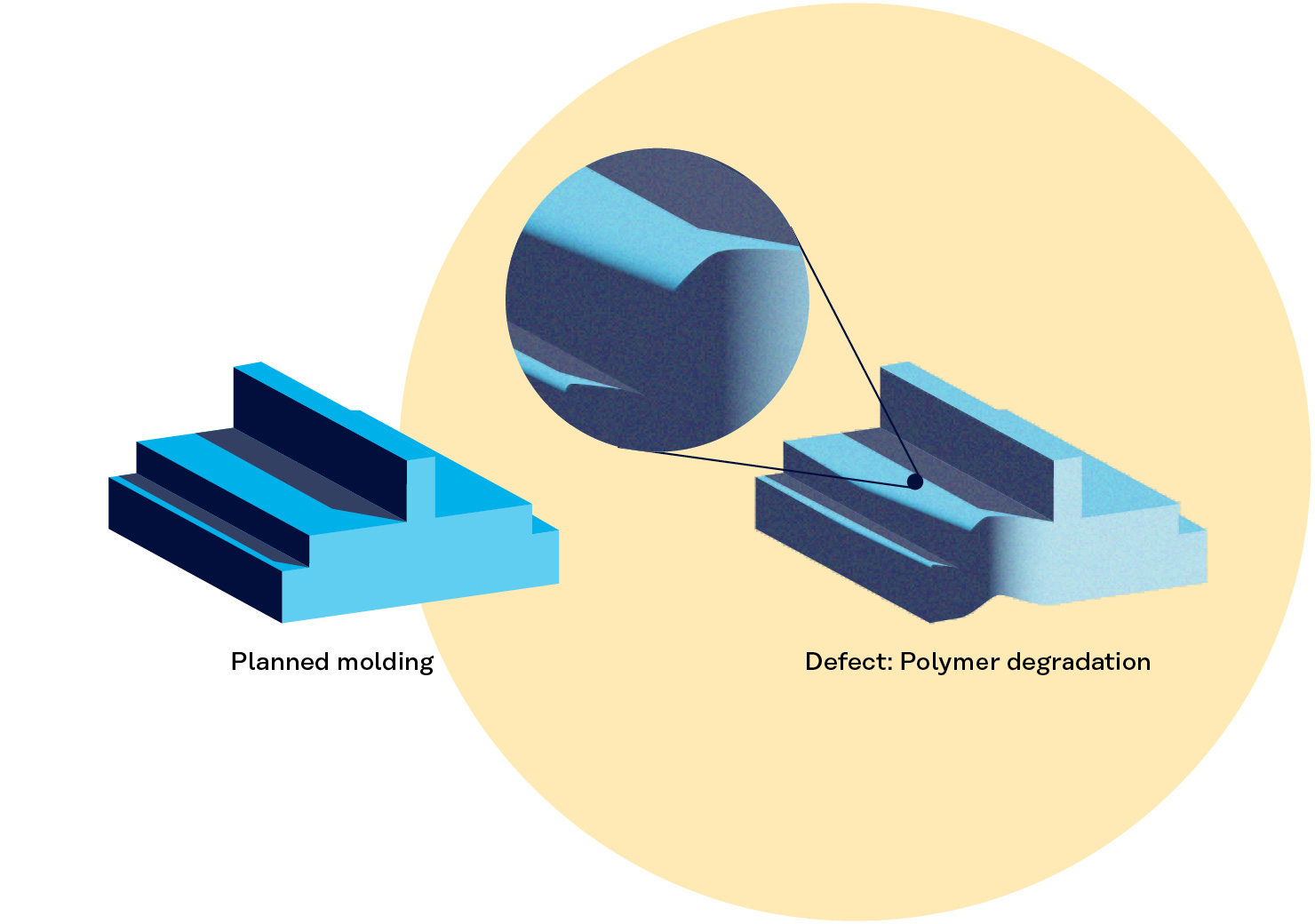
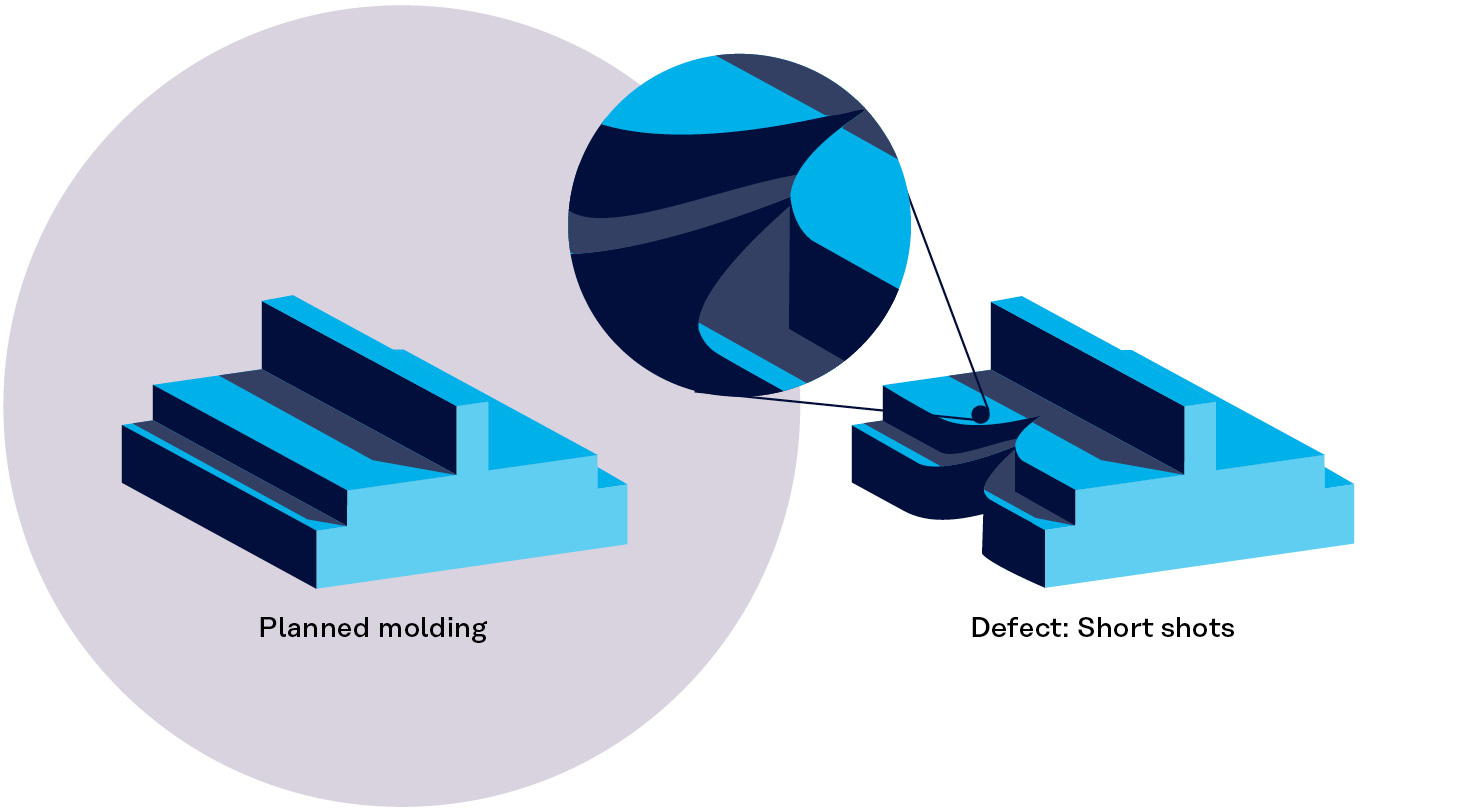
Defectos que dependen del equipo y del material
Puesto que el equipo y el material se afectan el uno al otro, es común tener defectos causados por ambos. Por ejemplo, las marcas de hundimiento pueden ser un defecto ocasionado por el equipo si la velocidad de enfriamiento es muy alta. Esto puede generar que la superficie de la parte se solidifique antes de que el material al centro tenga tiempo de fluir a su lugar. La otra opción puede ser un defecto generado por el material, ya que algunos materiales, como resinas de relleno o reforzadas, tienen mayor tendencia a encogerse y mostrar marcas de hundimiento.
Algunos ejemplos de defectos causados por el equipo que generan marcas del expulsor son mal diseño de molde (en especial respecto a compuertas), mal diseño del pin del expulsor o mantenimiento inadecuado del molde. Por otro lado, los defectos relacionados con el material como fragilidad o baja resistencia al impacto también pueden ocasionar marcas del expulsor.
Una vez más, es importante mencionar que esta lista de defectos y sus motivos está incompleta y solo buscamos presentar algunos ejemplos.
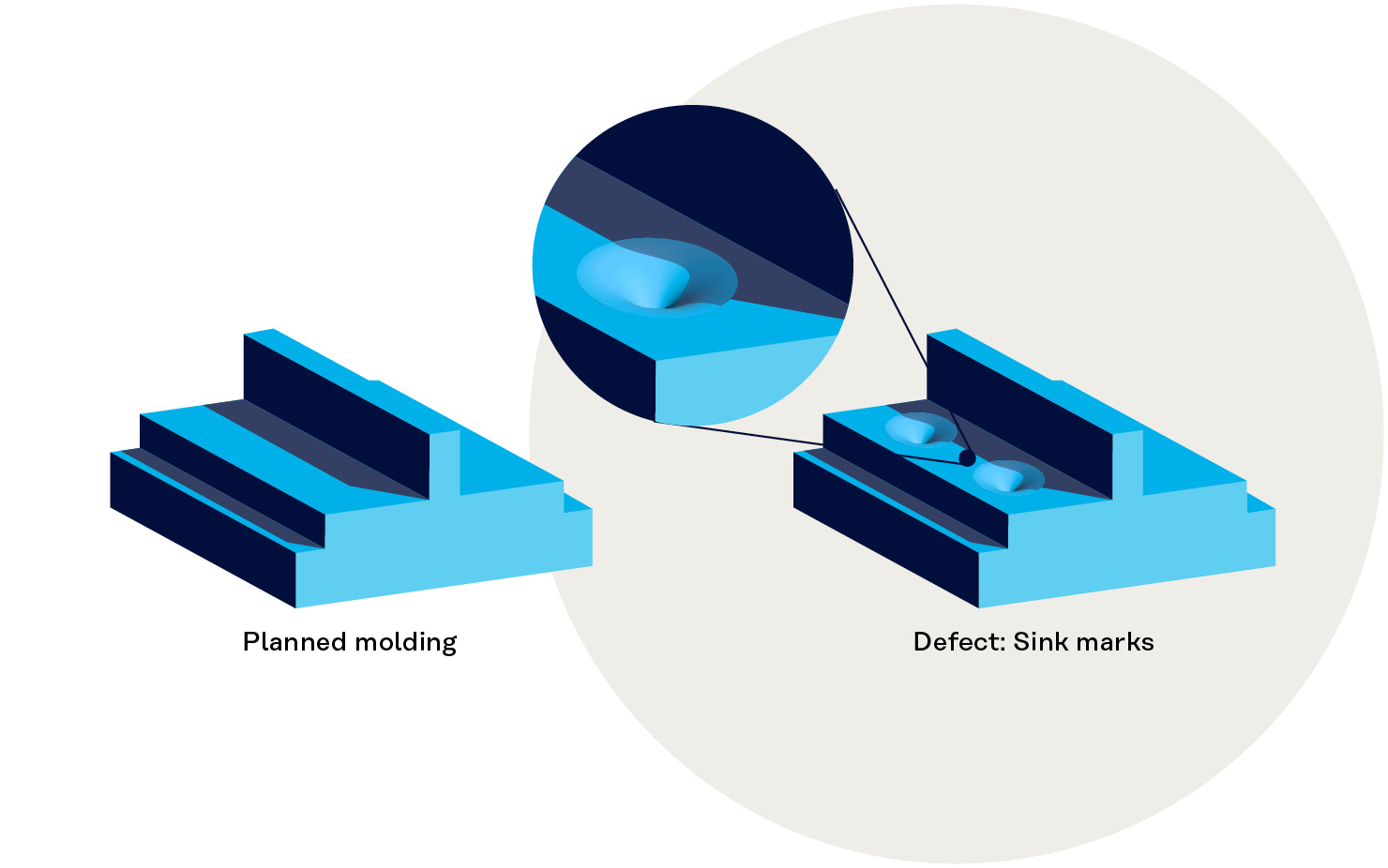
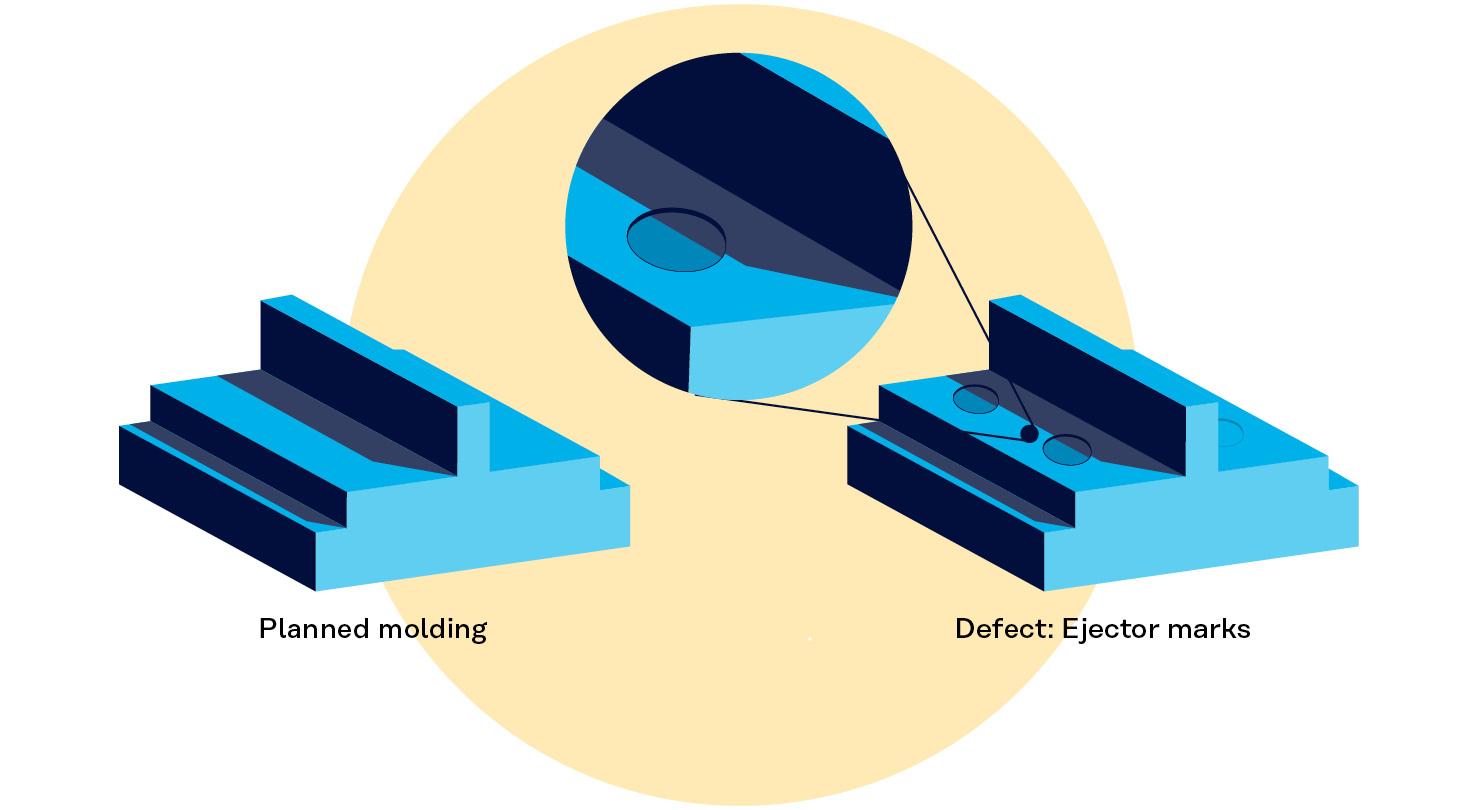
Datos útiles
Las materias primas de Kuraray son aditivos excelentes que ayudan a reducir los defectos de las partes moldeadas en el moldeo por inyección y pueden mejorar las propiedades relevantes de los materiales, como el flujo y la contracción.
Materiales de moldeo por inyección
Todos los termoplásticos, así como algunos termoestables y elastómeros son materiales adecuados para el moldeo por inyección.
Los termoplásticos usados con mayor frecuencia en el moldeo por inyección a nivel mundial son polipropileno (PP), acrilonitrilo butadieno estireno (ABS), polietileno (PE) y poliestireno (PS).
Como materiales “suaves” para moldeo por inyección 2K y 3K, los elastómeros termoplásticos (TPE) son procesados con más regularidad.
En más bien poco común usar termoestables en el moldeo por inyección, debido a su densidad de entrelazamiento y su incapacidad de volver a fundirse y volver a formarse. Sin embargo, algunos termoestables se usan como aditivos en ciertas aplicaciones, como mejorar las propiedades de las partes termoplásticas.
Los materiales normalmente están disponibles en pequeños pellets o como un polvo fino y en algunos casos son líquidos. Al añadir varios aditivos, las propiedades de las partes moldeadas o la procesabilidad del material pueden mejorar. Algunos ejemplos de aditivos incluyen colorantes para color o fibra de vidrio para mayor rigidez; sin embargo, también hay aditivos más avanzados, como los elastómeros de especialidad de Kuraray.
Cada material requiere diferentes parámetros durante el procesamiento para lograr las partes moldeadas deseadas; estos incluyen temperatura y presión de inyección, temperatura de molde y expulsión, así como tiempo del ciclo. Dependiendo de cómo se establecen estos parámetros, la apariencia, dimensiones y propiedades mecánicas de las partes moldeadas cambian de manera considerable. Además de la tecnología adecuada, se requiere mucha experiencia.
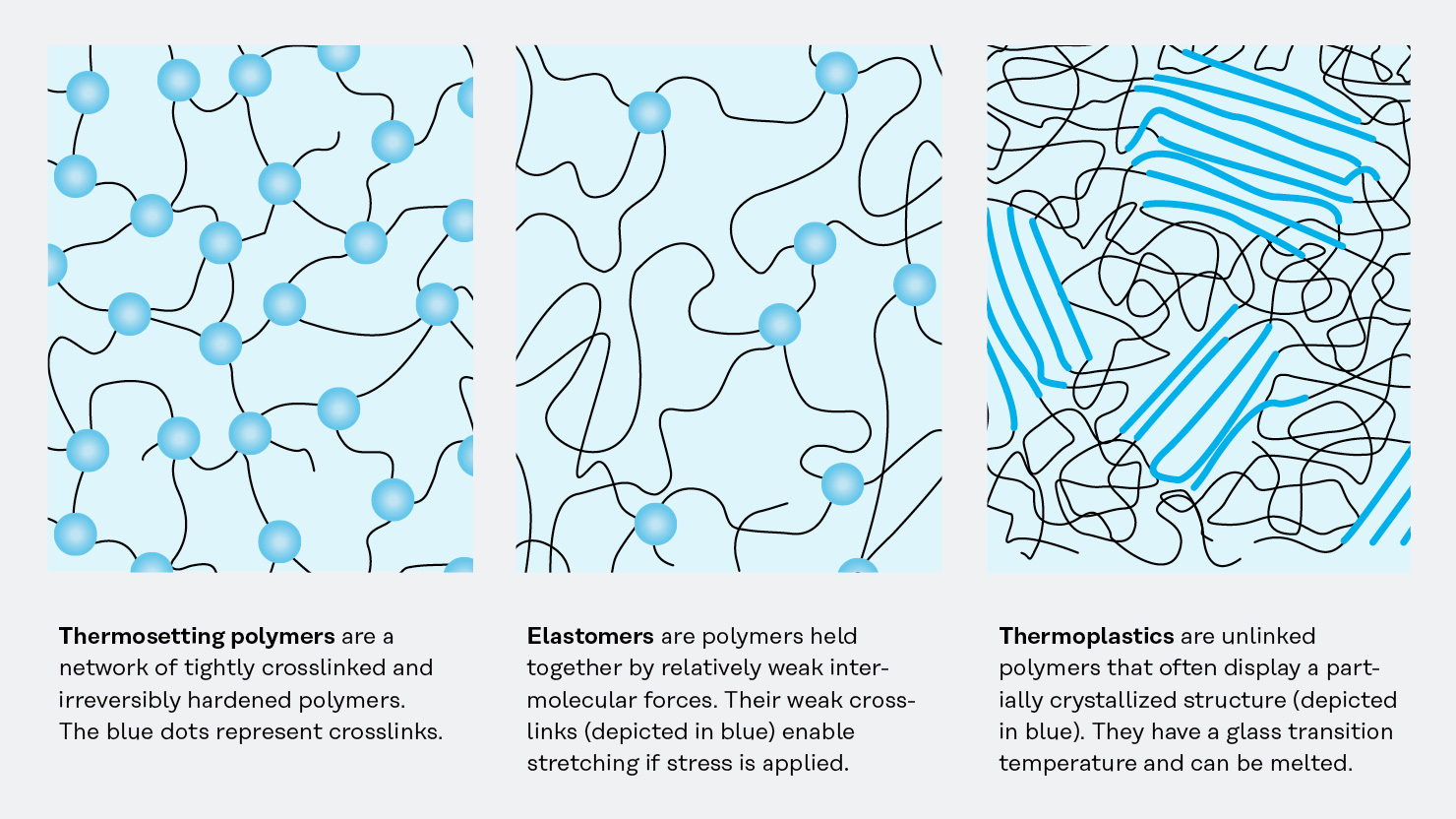
Elastómeros termoplásticos
Los elastómeros termoplásticos (TPE) son materiales con una elasticidad similar al caucho y la procesabilidad de los termoplásticos. En otras palabras, pueden estirarse como una liga y fundirse y moldearse en una gran variedad de formas y tamaños. Después de enfriarse, conservan su elasticidad. Si es necesario, pueden volver a fundirse y volver a moldearse tiempo después, lo cual implica menos desecho de material en el procesamiento.
La procesabilidad de los elastómeros termoplásticos los hace un excelente material para el moldeo por inyección. A diferencia del caucho, no requieren vulcanización, un método de procesamiento del caucho que exige mucho tiempo. Debido a sus diversas aplicaciones, son un material muy adecuado para muchas industrias y propósitos.
Para conocer más sobre las propiedades materiales de diferentes tipos de elastómeros termoplásticos, consulte la siguiente tabla.
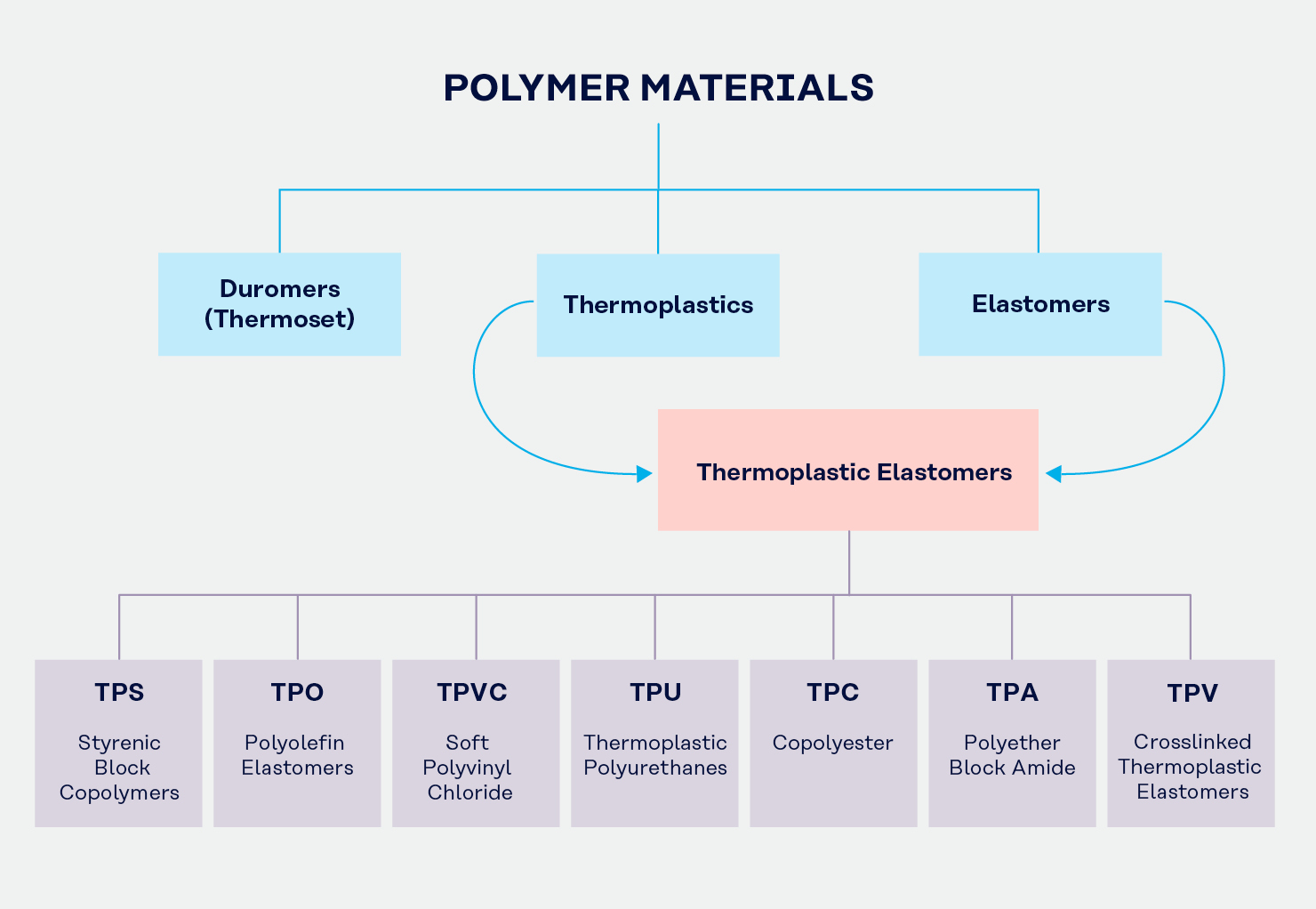
Propiedades/Materiales | TPS | TPO | TPVC | TPU | TPC | TPA |
Dureza Shore | 30A 〜 70A | 60A 〜 95A | 40A 〜 70A | 80A 〜 80D | 90A 〜 70D | 40D 〜 65D |
Resistencia a la tracción (MPa) | 9.8 〜 34.3 | 2.9 〜 18.6 | 9.8 〜 19.6 | 29.4 〜 49 | 25.5 〜 39.2 | 11.8 〜 34.3 |
Elongación (%) | 500 〜 1,200 | 200 〜 600 | 400 〜 500 | 300 〜 800 | 350 〜 450 | 200 〜 400 |
Resiliencia por rebote (%) | 45 〜 75 | 40 〜 60 | 30 〜 70 | 30 〜 70 | 60 〜 70 | 60 〜 70 |
Densidad (g/cm³) | 0.91 〜 0.95 | 0.88 | 1.2 〜 1.3 | 1.1 〜 1.25 | 1.17 〜 1.25 | 1.01 |
Resistencia a la abrasión | Suficiente | Malo | Suficiente | Excelente | Suficiente | Bueno |
Resistencia a la flexión a temperatura ambiente | Bueno | Suficiente | Bueno | Bueno | Excelente | Excelente |
Resistencia al calor | 〜 80°C | 〜 120°C | 〜 100°C | 〜 100°C | 〜 140°C | 〜 100°C |
Resistencia al aceite | Malo | Suficiente | Bueno | Excelente | Excelente | Excelente |
Resistencia a la intemperie | Malo-bueno | Bueno | Suficiente-bueno | Suficiente-bueno | Suficiente | Bueno |
Temperatura de fragilidad | < -70°C | < -70°C | -50°C 〜 -30°C | < -70°C | < -70°C | < -70°C |
Aplicaciones | Calzado, mezclas de reina, adhesivos, modificación de asfalto | Mangueras/tubos automotrices, productos de consumo | Automotriz, cables eléctricos, ingeniería civil/construcción | Calzado, productos industriales, productos de consumo, productos médicos | Automóviles, electrónicos, productos industriales | Productos deportivos, productos industriales |
Elastómeros termoplásticos de Kuraray
Kuraray ofrece plásticos de alta gama para moldeo por inyección, a fin de lograr mejores propiedades materiales. Ya sea para partes completas o como remplazo de caucho/PVC flexible, las propiedades clave de estos plásticos añaden valor real a sus productos y los ayudan a hacer sus procesos más eficientes.
Los materiales de Kuraray facilitan la producción eficiente de componentes plásticos a gran escala. Para el moldeo por inyección 2K, Kuraray ofrece elastómeros termoplásticos de alta gama que pueden servir como componentes funcionales suaves.
SEPTON™
SEPTON™ es una serie de elastómeros termoplásticos estirénicos desarrollada por Kuraray. Los Copolímeros de bloque estirénico hidrogenados (HSBC) se componen de bloques duros de estireno y un bloque blando de dieno hidrogenado. Los HSBC presentan elasticidad tipo caucho, ya que el bloque duro actúa como un punto de reticulación por debajo de la temperatura de transición vítrea del poliestireno y el bloque blando brinda elasticidad. La hidrogenación genera excelente resistencia al calor y a la intemperie.
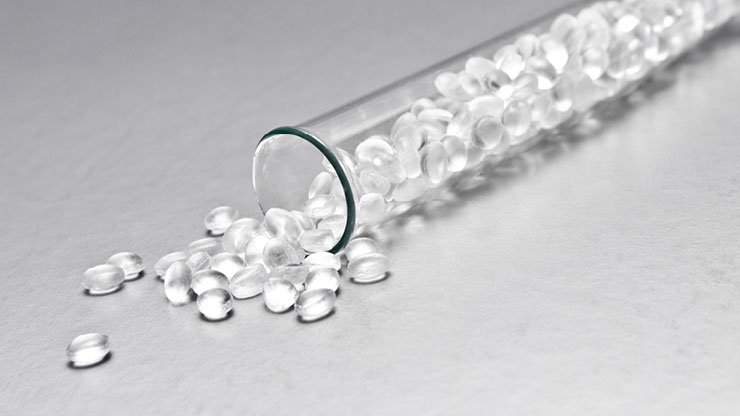
Beneficios
Al añadir SEPTON™ y plastificante a las poliolefinas, se puede lograr buena capacidad de moldeo por inyección y partes moldeadas flexibles.
Al usar los grados SEEPS de SEPTON™, se mejora la transferencia del relieve y también la adhesión en moldeo por inserto.
SEPTON™ BIO-series
Con SEPTON™ BIO-series, Kuraray ofrece un exclusivo copolímero de bloque de farneseno estireno hidrogenado (HSFC), que nos coloca como el primer y único fabricante de materiales HSBC biológicos en el mercado. El elastómero termoplástico SEPTON™ BIO-series representa una nueva solución para los fabricantes que crea nuevos compuestos y usos finales con un alto contenido de base biológica, a fin de expandir áreas existentes del mercado y abrir nuevas áreas.
Para conocer los beneficios adicionales, favor de consultar la sección anterior sobre SEPTON™ o contactar al área de ventas.

HYBRAR™
HYBRAR™ es un copolímero de tribloque verdaderamente exclusivo que tiene bloques de poliestireno y un bloque intermedio de polidieno con alto contenido de enlaces de vinilo. Debido a su tangente delta máxima cerca de la temperatura ambiente, HYBRAR™ presenta un alto nivel de amortiguación a la vibración y propiedades de absorción de impacto, incluso sin el plastificante integrado. Estos elastómeros termoplásticos están disponibles como grados hidrogenados y grados no hidrogenados duraderos.
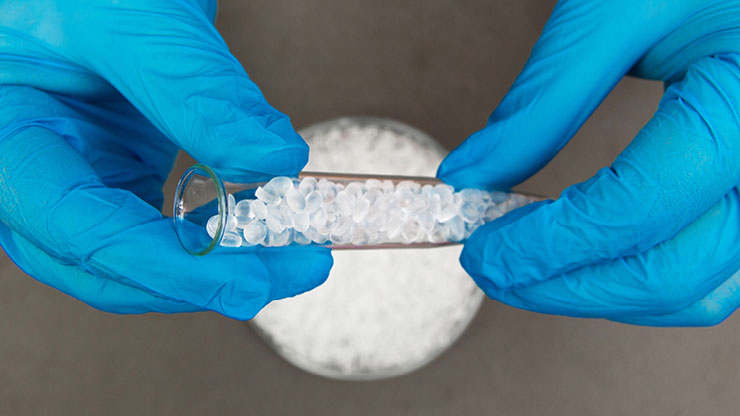
Beneficios
Al añadir una pequeña cantidad de HYBRAR™ al polipropileno, se reduce la cristalinidad y la transparencia mejora.
Cauchos líquidos
Los cauchos líquidos son de gran uso como “plastificantes reactivos” o modificadores en caucho y plástico y también se pueden usar en el moldeo por inyección. Los cauchos líquidos son polímeros líquidos con menor peso molecular y tienen la misma estructura química que el caucho sólido.
Los cauchos líquidos están en estado líquido a temperatura ambiente, mientras que presentan propiedades similares al caucho tras la elongación de cadena y reticulación. Algunos ejemplos de cauchos líquidos incluyen:
- cauchos líquidos de dieno como cauchos líquidos de butadieno, cauchos líquidos de isopreno y cauchos líquidos de estireno-butadieno
- cauchos líquidos de silicona
- cauchos líquidos de olefina
- cauchos líquidos de uretano
KURARAY LIQUID RUBBER
La KURARAY LIQUID RUBBER es un caucho líquido con entrelazamiento que se compone de caucho líquido de butadieno (L-BR), caucho líquido de isopreno (L-IR) y caucho líquido de estireno-butadieno (L-SBR). Los cauchos líquidos son incoloros, transparentes, casi completamente inodoros y tienen valores de COV bajos. Los polímeros de butadieno, isopreno y estireno tienen un bajo peso molecular que se establece entre el caucho sólido y el plastificante.
Los productos de KURARAY LIQUID RUBBER son diseñados como “plastificantes reactivos”, es decir: en el proceso de mezclado de caucho altamente demandante de tiempo y energía, ayudan a reducir la viscosidad de Mooney y facilitan el proceso de mezclado. Lo anterior genera un aumento de flujo en el compuesto, así como menor tiempo requerido y menores costos de procesamiento.
Asimismo, los productos de KURARAY LIQUID RUBBER son co-vulcanizables con el caucho base a fin de evitar la migración. La migración reducida mejora significativamente la vida en anaquel y la duración de los productos.
KURARAY LIQUID RUBBER es muy adecuada para el moldeo por inyección de compuestos de caucho.
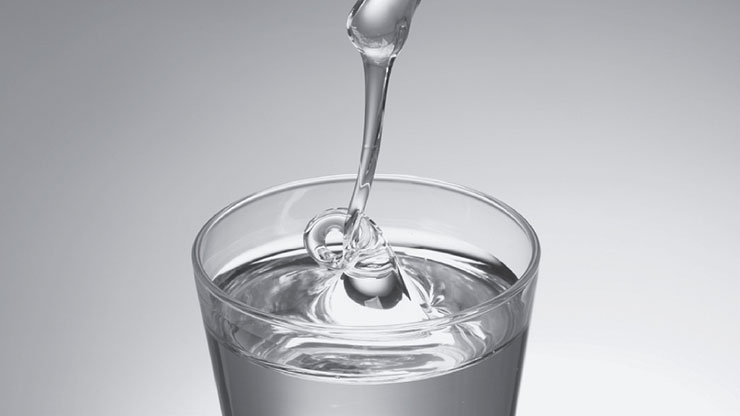
Beneficios
KURARAY LIQUID RUBBER puede mejorar el proceso de moldeo por inyección de los compuestos de caucho en diversas formas:
- Flujo: como ayuda en el procesamiento, reduce la viscosidad de fundido y hace a los compuestos de caucho más fluidos y más fáciles de inyectar en la cavidad del molde, lo cual permite al material llegar a esquinas muy apretadas de la cavidad del molde y mejorar visiblemente la superficie, generando así una réplica más precisa del molde.
- Menor consumo de energía: un mejor flujo del compuesto incrementa la eficiencia del proceso de mezclado y moldeo de manera significativa. KURARAY LIQUID RUBBER puede ayudar a reducir la temperatura de moldeo, lo cual reduce a su vez el consumo de energía.
- Propiedades y rendimiento: KURARAY LIQUID RUBBER puede aumentar las propiedades y el rendimiento de los productos finales de caucho, es decir la resistencia a la abrasión y la flexibilidad a bajas temperaturas. Asimismo, KURARAY LIQUID RUBBER puede reducir la migración y mejorar la vida en anaquel y la durabilidad de los productos finales de caucho en comparación con los plastificantes normales.
Datos útiles
La cantidad óptima de KURARAY LIQUID RUBBER que debe añadirse al compuesto de caucho depende de diversos factores. ¡Contáctenos para conocer más sobre cómo puede lograr mejores resultados en el moldeo por inyección con KURARAY LIQUID RUBBER!
Liquid farnesene rubber
¿Usted valora la sustentabilidad?
El liquid farnesene rubber (LFR) está hecho a base de materias primas naturales y renovables: contiene una forma polimerizada de beta-farneseno, un monómero renovable. Mediante procesos de fermentación establecidos, las exclusivas cepas de levadura convierten las fuentes de azúcar, como la caña de azúcar, en beta-farneseno.
El liquid farnesene rubber funciona como un plastificante reactivo con un peso molecular más alto que los plastificantes normales. El liquid farnesene rubber es co-vulcanizable y reduce la migración de manera importante, con lo que se genera una mejora en la durabilidad de los compuestos de caucho.
¿Quisiera saber más sobre nuestros productos y sus excelentes capacidades de procesamiento? Contacte a su representante de Kuraray.
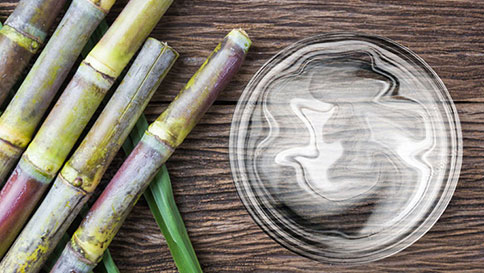
Otros materiales
Además de los plásticos, se puede usar una gran variedad de materiales para el moldeo por inyección, como los metales. Sin embargo, el proceso de moldeo por inyección para metales por lo general se conoce como fundición a presión.
Moldeo por inyección: ventajas
La principal ventaja del moldeo por inyección es la producción de partes en grandes cantidades. El rango de aplicaciones se extiende de pequeños lotes de varios cientos de piezas a producción masiva con cantidades de varios millones de componentes.
Una vez que la inversión inicial se ha amortizado, el precio unitario es extremadamente bajo con este proceso de manufactura. Conforme aumenta el número de unidades, el costo unitario puede bajar de manera importante, lo que hace que el proceso sea muy productivo.
Otras ventajas del moldeo por inyección incluyen gran repetibilidad y tolerancias, amplia gama de materiales, bajos índices de desecho y apariencia visual atractiva de las partes moldeadas.
Desventajas
Una desventaja importante del moldeo por inyección son los altos costos de arranque relacionados con la construcción de moldes.
También puede ser costoso si se requieren cambios en el diseño de los moldes para adaptarlos al proceso, o si ocurren errores de diseño. Incluso los pequeños errores pueden generar altos costos.
Otras desventajas incluyen tiempos más largos de arranque y posibles limitaciones con moldes más grandes.
Aplicaciones
El moldeo por inyección se emplea en una gran variedad de industrias, como de productos de consumo (cepillos dentales), muebles (sillas), automotriz (tableros de instrumentos), electrónicos (armazones de herramientas eléctricas), juguetes (bloques de construcción plásticos), cuidado a la salud (jeringas), embalajes (taparroscas) y muchos más.
Historia
El inventor del moldeo por inyección es el estadounidense John Wesley Hyatt, quien patentó la primera máquina de moldeo por inyección junto con su hermano, Isaiah, en 1871. En esos tiempos, consistía en una máquina muy sencilla en la que se inyectaba plástico mediante un cilindro caliente a un molde con la ayuda de un pistón y se usaba para fabricar productos como botones, peines y bolas de billar.
En 1903, los químicos alemanes Arthur Eichengrün y Theodore Becker inventaron las primeras formas solubles de acetato de celulosa, que podías moldearse fácilmente por inyección en forma de polvo. Fue también Eichengrün quien desarrolló la primera prensa de moldeo por inyección en 1919 y, dos décadas más tarde, patentó el moldeo por inyección de acetato de celulosa plastificado.
Durante la Segunda Guerra Mundial, la industria creció de manera importante debido a la alta demanda de productos masivos económicos. En 1946, el estadounidense James Watson Hendry hizo un desarrollo revolucionario con la primera máquina de moldeo por inyección mediante tornillo. Esto no solo permitió mucho más control preciso de la velocidad de inyección y la calidad de las partes moldeadas, sino también permitió que el material se mezclara antes de la inyección.
Otro desarrollo de Hendry de la década de 1970, el proceso de moldeo por inyección asistido por gas, permitió la producción de artículos complejos y huecos y mejoró de manera significativa la flexibilidad de diseño, la resistencia y el acabado de superficie de las partes moldeadas por inyección.
Hoy en día, el moldeo por inyección es un mercado mundial con ventas anuales de cientos de miles de millones de dólares y a nivel mundial, cerca de 55 millones de toneladas de plástico se procesan con este método cada año.
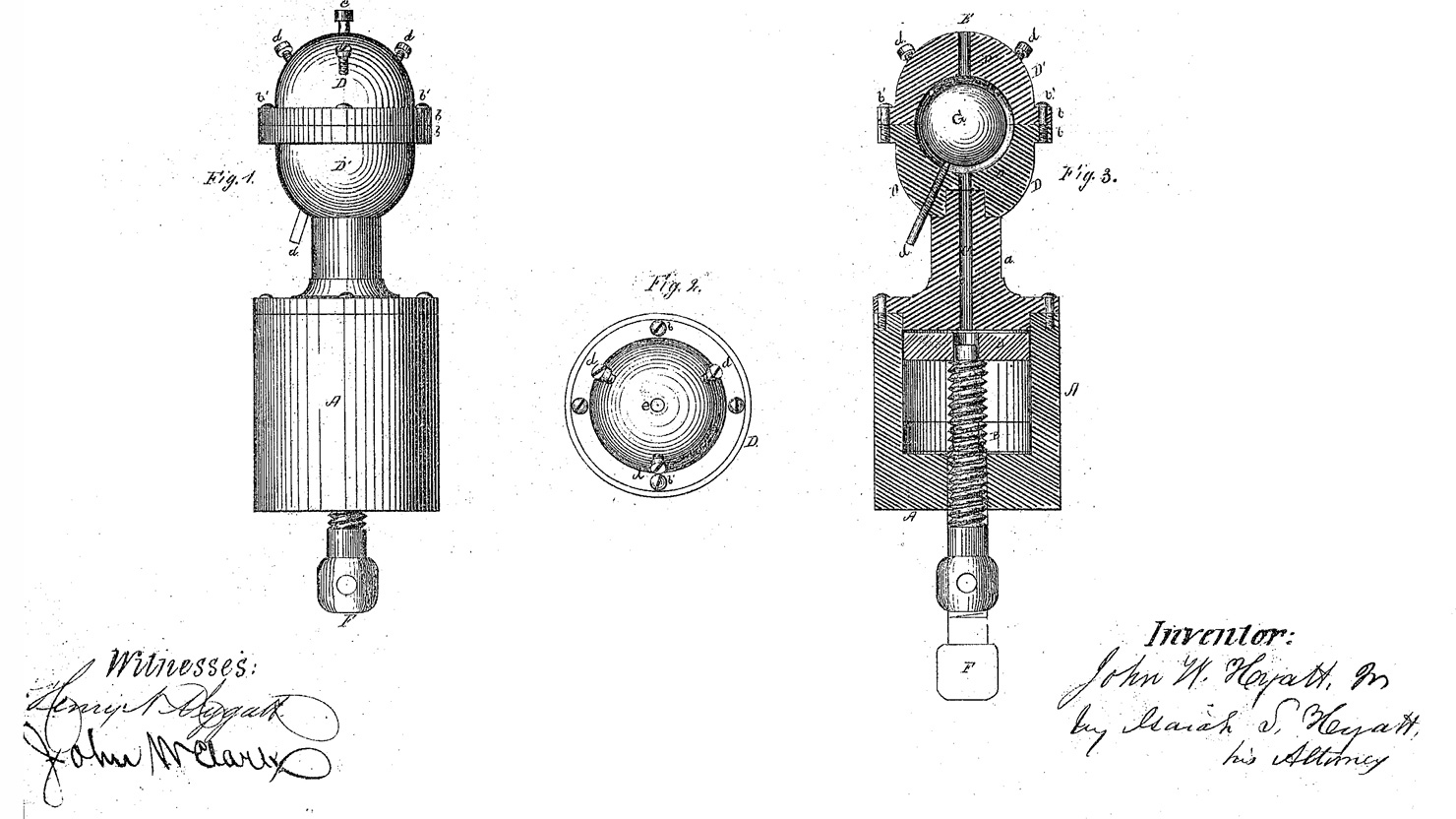
Patente US114945: moldeo por inyección de celuloide en bolas de billar, 16 de marzo de 1871
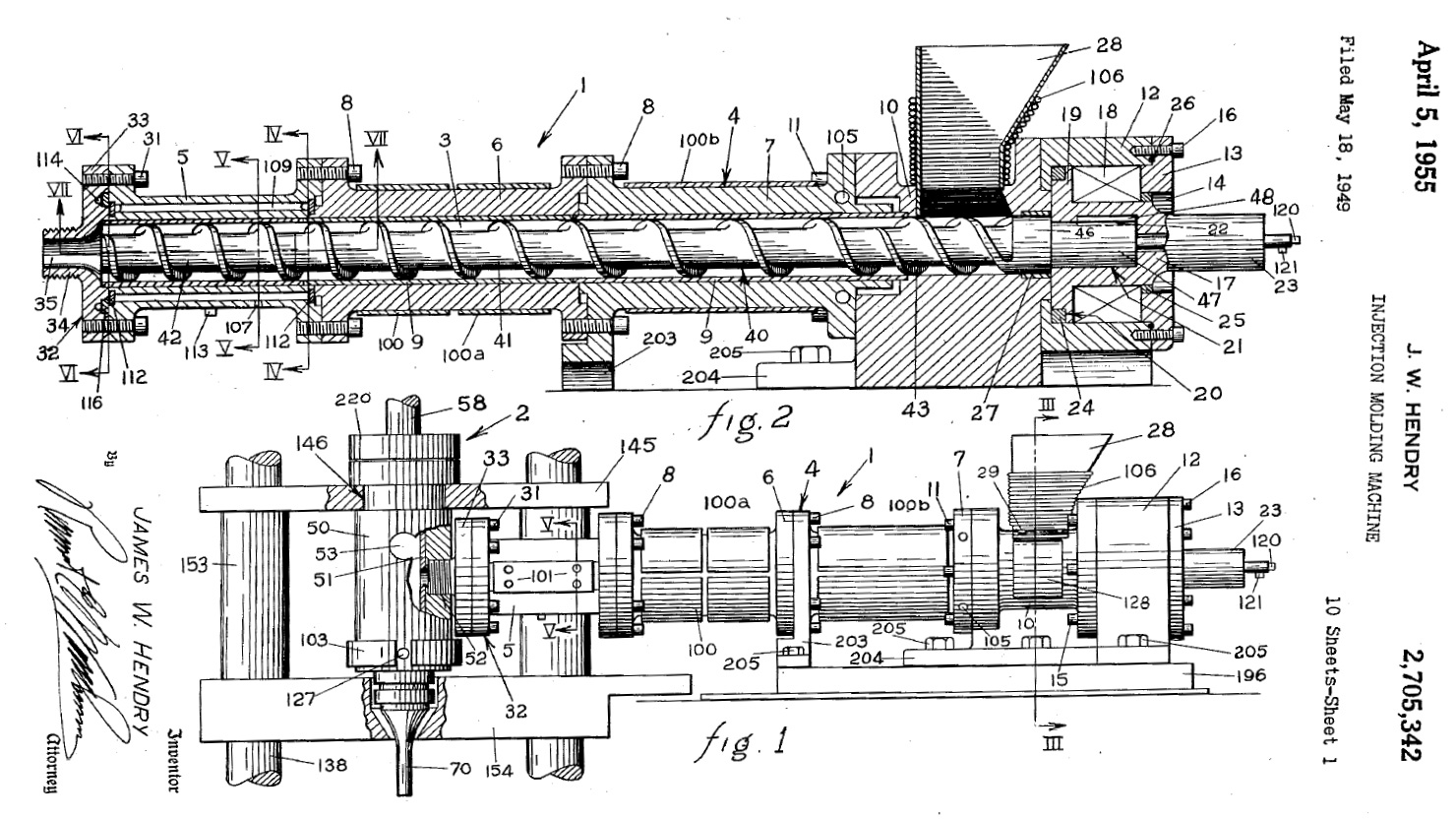
Dibujos de la patente para la máquina de moldeo por inyección mediante tornillo de James Watson Hendry
Estándares y certificaciones
Existen varias certificaciones que pueden confirmar la calificación de su proveedor de servicio de moldeo por inyección. La certificación ISO 9001 es de particular importancia.
La Sociedad de la Industria de los Plásticos (SPI) ha definido también normas para la calidad óptica de los plásticos para la industria de plásticos de los Estados Unidos. Las normas definen las cualidades de superficie de las partes plásticas moldeadas por inyección, haciendo una distinción entre doce diferentes cualidades de superficie en cuatro categorías.
Costos
El moldeo por inyección ofrece ventajas importantes para la producción de partes moldeadas en grandes volúmenes; sin embargo, cualquier individuo que elija este proceso debe conocer los costos de arranque. La inversión inicial puede ser muy alta. Además de la máquina de moldeo por inyección, los costos para los moldes son significativos y a veces pueden implicar millones.
Esto puede ser de su interés: Kuraray le apoya en el desarrollo de compuestos para ciclos más rápidos y producción optimizada para lograr la mayor rentabilidad posible del proceso de moldeo por inyección.
¿Tiene una idea clara del producto que quiere producir, pero no está seguro de la receta y composición de los materiales? Entonces, le sugerimos contactar a su representante de Kuraray. Con gusto le ayudaremos compartiéndole nuestro conocimiento sobre el proceso y el material y nuestro apoyo en la organización de su cadena de suministro, si así lo requiere.
Contacto para negocios
¡Estaremos a la espera de sus dudas!
Contacto