What is plastic recycling?
Plastic recycling is the processing of plastic waste into useful products, including new plastic and chemical feedstocks.
Because plastics are a wide and adaptable class of materials with varying chemical compositions, there’s no universal recycling process. Instead, they must be sorted, cleaned, and recycled through one of several different processes. Although this can be complicated and expensive, plastic recycling is a rapidly growing area of research that is increasingly intertwined with the future of manufacturing.
Why is it important to recycle plastics?
Since the beginning of the Plastic Age in 1950, industries ranging from consumer goods to construction have become increasingly reliant on plastic as an inexpensive, adaptable material for almost any application.
But the widespread use of fossil-based plastics, which are non-biodegradable and non-renewable, has far-reaching consequences. The plastic waste people produce is here to stay, collecting in the ecosphere, landfills, groundwater, and oceans.
By recycling plastic, manufacturers and consumers prevent widespread pollution, conserve energy, and reduce emissions. When we reuse existing plastic, we conserve limited oil reserves, protect ecosystems, and even create jobs. As sustainability becomes increasingly important, so does plastic recycling.
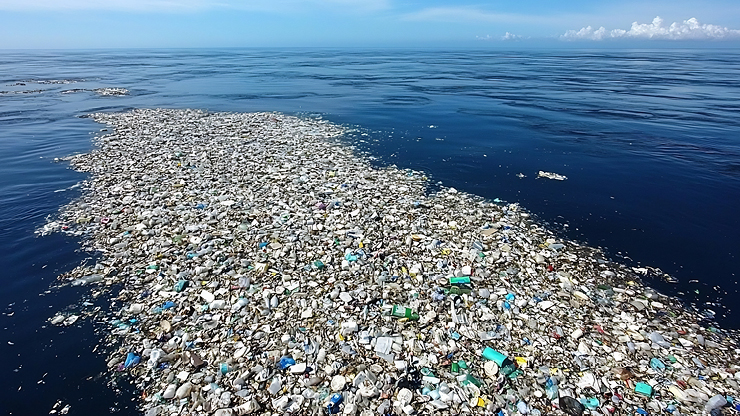
Plastic recycling: Facts and figures
Although recycling is on the rise, most plastic waste is not recycled. Incineration and landfills remain the most common methods of handling plastic waste.
- As of 2015, 6,300 million metric tons of plastic waste had been generated (Geyer et al., 2017).
- Of that waste, only 9% was recycled. 12% was incinerated, and the remaining 79% has accumulated in landfills or the natural environment (Geyer et al., 2017).
- Only 1% of all plastic has been recycled more than once (Geyer et al., 2017).
- In 2021 in the EU, 16.13 million tons of plastic waste were generated, of which 6.56 million tons were recycled—that’s 40.7% (European Parliament, 2024).
- But this figure is only a small improvement over 2011, when 36.4% of the EU’s plastic waste was recycled (European Parliament, 2024).
- Plastic waste production in the EU increased from 12.48 million tons to 16.13 million tons from 2011 to 2021, an increase of 29.2% (European Parliament, 2024).
- European leaders in recycling include Iceland, Germany, and Italy, with 20.7, 19.9, and 18.3 kilograms per capita respectively (European Parliament, 2024).
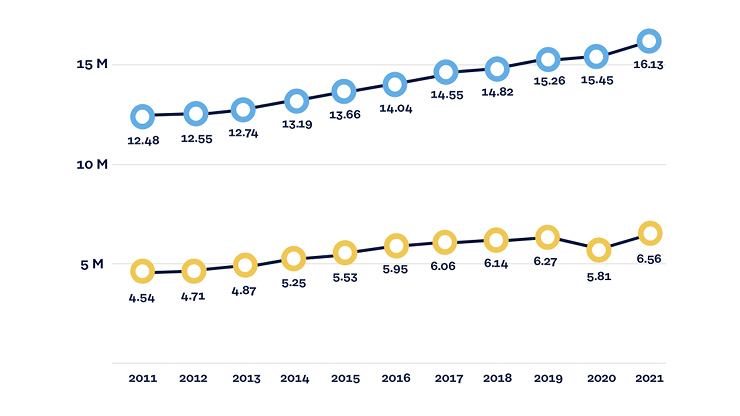
How plastic recycling works: An overview
The recycling process has three main steps: collection, sorting, and processing.
- Collection: Pieces of plastic waste marked with resin identification codes are collected through government programs, businesses, and waste management facilities. The collected plastic waste is then sent to recycling plants.
- Sorting: First, non-plastic waste is separated from plastic waste. Then, the plastic waste is sorted by type, since each type must be processed separately. Sorted plastic that is destined to be recycled is washed to remove adhesives, food residue, and other waste. The remaining plastic is sent to a landfill or incinerator.
- Processing: Waste plastic is processed very differently depending on its chemical composition, its intended use, its quality, its purity, and the facility. In the next section, we cover all of the types of plastic recycling in use and in development today.
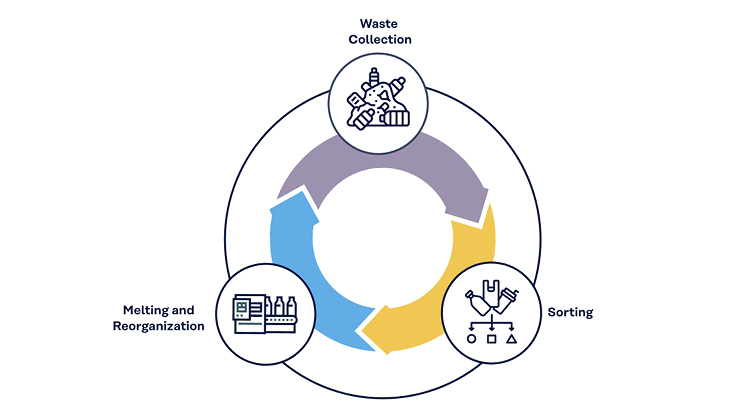
Types of plastic recycling
Although most of the plastic recycling that occurs today is mechanical, other approaches to the recycling process are a rapidly growing area of research and commercialization.
Mechanical recycling
Any thermoplastic, or plastic that can be melted and reformed repeatedly, can be mechanically recycled. In this process, plastics are sorted, shredded, and washed before being melted into uniform pellets that can be used to manufacture new products through processes like injection molding. Sorting methods may vary widely, and facilities typically keep some plastic types for recycling and dispose of others.
Since almost every plastic in widespread use is thermoplastic, mechanical recycling is the most well-explored approach. Polyethylene terephthalate (PET), high-density polyethylene (HDPE), and polypropylene (PP) are often recycled mechanically.
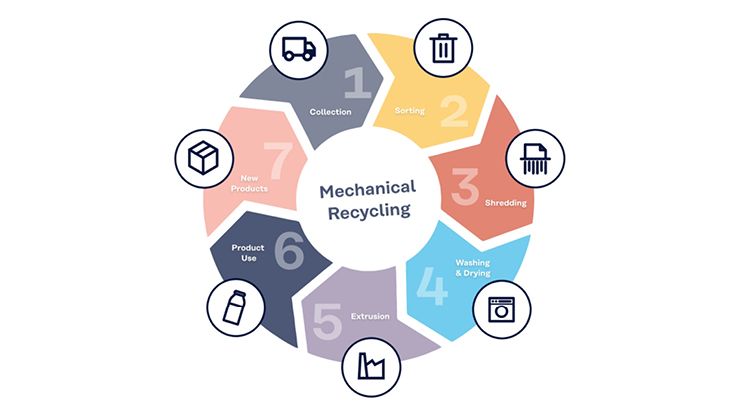
Chemical recycling (aka feedstock recycling)
This method smooths over the additives, impurities, and weathering in waste plastic by depolymerizing it into base monomers, or feedstocks, that can be used to manufacture new virgin plastic. This process, which can be thermal or chemical, is typically energy-intensive and has only been commercialized for polyethylene terephthalate (PET), polystyrene (PS), and polyurethane (PU). As a result, although chemical recycling is a developing field, mechanical recycling remains more common.
Some methods of chemical recycling, like pyrolysis, hydro-cracking, and gasification, convert the waste plastic into liquid or gaseous fuels rather than feedstocks for new plastic. These processes, in some cases, are less energy-efficient than fossil fuels, produce emissions and do not seem to be economically competitive yet.
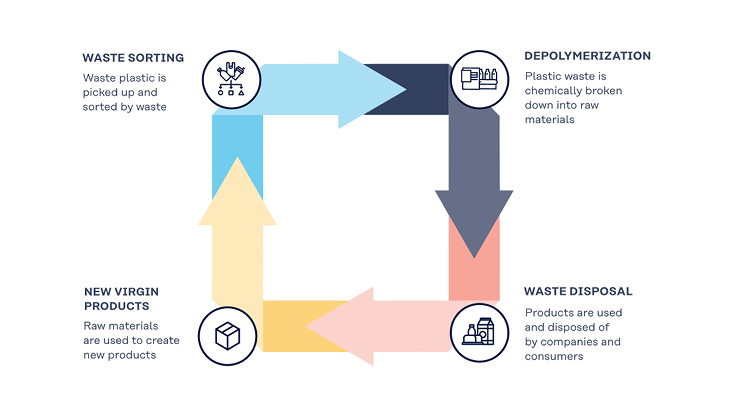
Dissolution recycling
When plastic waste is mixed or impractical to sort, individual plastic types can be selectively dissolved and recovered through dissolution recycling. In this process, mixed plastic waste is placed in a solvent that will only dissolve a single type of polymer. The solvent containing the dissolved plastic can then be separated, isolating a particular material from the mixed waste without changing its polymer structure.
This method is suitable for even contaminated, unsorted plastic, and it enables the recovery of some plastics that cannot be mechanically recycled. Currently, industrial procedures exist that allow polyvinyl chloride (PVC), polystyrene (PS), polypropylene (PP), polycarbonate (PC), and nylon (PA) to be recovered through dissolution recycling.
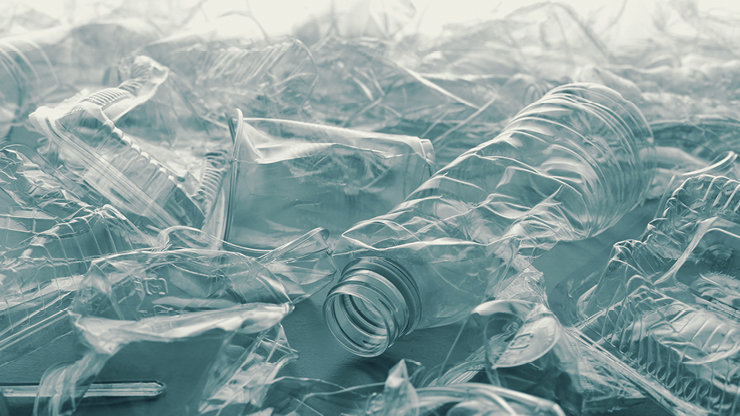
Organic recycling: Biodegradation & composting
Organic recycling takes advantage of controlled biological processes to break down plastic polymers into useful byproducts. These processes can be initiated by bacteria, artificially produced enzymes, and even worms. Although organic recycling methods do not always recycle waste into usable plastic or polymer feedstocks, they produce other potentially useful compounds and prevent plastic pollution.
Anaerobic digestion
This existing process was originally designed for the conversion of plant matter, manure, and food waste into biogas. In anaerobic digestion systems, a tailored mix of microorganisms breaks down waste into compounds that can be used as fuel, compost, or fertilizer. Research has identified bacteria that can break down various plastics under anaerobic conditions, making this technology a potential approach to recycling.
Composting
Although the most common plastics used today were not designed to be compostable, certain organisms may make it possible. A species of wax worm, for example, has a gut microbiome that allows them to successfully eat and digest polystyrene, a top-polluting plastic with a lifespan of over 500 years.
Most approaches to plastic composting apply only to specific types of plastic or bio-based polymers and are only effective in industrial composting conditions where the temperature and microbiome are carefully controlled—plastic generally can’t be composted at home. But researchers hope that by isolating the enzymes that allow organisms like wax worms to digest plastic, they can identify new approaches to chemical recycling.
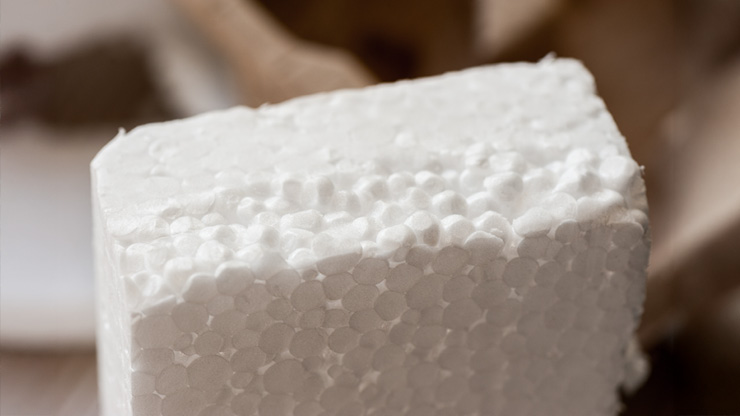
Incineration with energy recovery
Although many agencies don’t consider energy recovery to be a method of recycling, this is the fate of much of our recyclable plastic waste. In this approach, waste is burned instead of fossil fuels to generate energy.
Since all plastics release toxic fumes when burned, these plants must carefully regulate their emissions—but not all of them do. Even well-regulated incineration facilities produce carbon emissions and fail to recover any material for future use. The complex process of plastic sorting is also still necessary, as certain plastic types will release fumes that will damage equipment when burned.
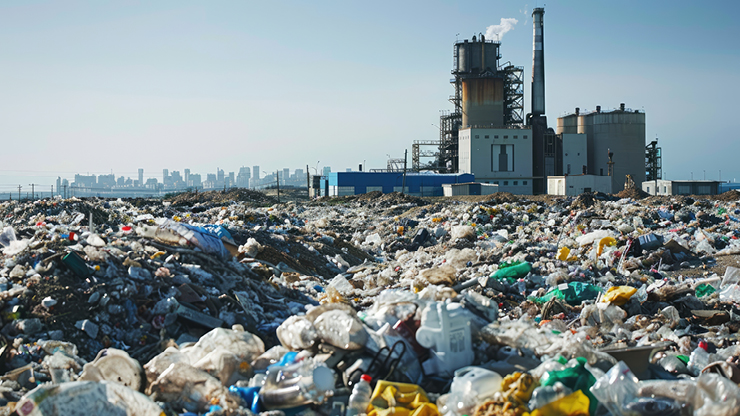
Obstacles to plastic recycling
Every type of plastic has a unique chemical makeup and polymer modifications that present unique challenges to the recycling process. While this complexity has limited the effectiveness of recycling for decades, recent advances have offered the industry new ways to surmount many of these obstacles.
Collecting and sorting plastics
Because plastic products use a wide variety of base polymers that have various additives, melting points, colors, and physical properties, they must be carefully sorted before they are recycled to ensure that the final product is suitable for use in manufacturing. This is an especially important step for mechanical recycling, which accounts for the bulk of plastic recycling.
Although resin identification codes are intended to enable sorting, they are often hard to read, incorrect, or missing—and hand-sorting plastic waste is not an economically viable approach. The difficulty of this first step in the recycling process was formerly one of the largest obstacles to widespread commercialization.
Advancements in sorting plastics are crucial to increasing the share of plastic waste that is recycled. Many are technological, such as sifters and scanners that can separate plastics by type and weight. Some are also organizational, such as collecting pre-separated plastic waste rather than mixed plastic waste.
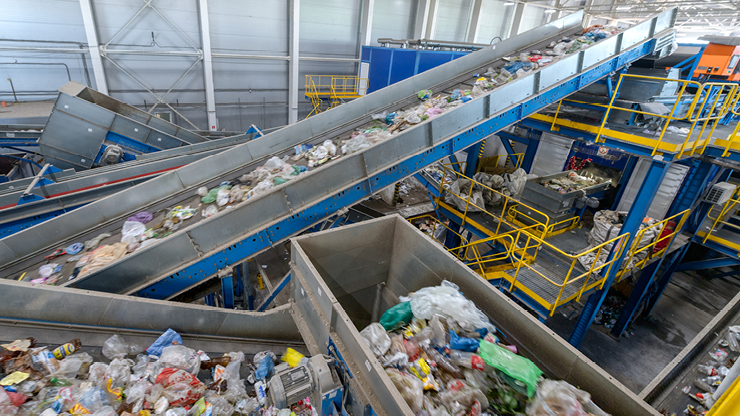
Economic viability and plastic quality
Sorting plastic waste and ensuring the purity and quality of recycled plastic are significant logistical and financial challenges. The physical properties of plastics degrade over time, each piece of plastic waste has experienced different conditions over its lifetime, and sorting systems can’t account for the thousands of different additives used to modify the plastics they’re combining.
As a result, the strength, elasticity, chemical composition, color, and overall quality of recycled plastic can be unpredictable, even with highly accurate sorting and quality control—which are expensive to implement. These challenges typically lead to either lower quality or higher cost in recycled plastics, both of which are unattractive options to manufacturers that can already source virgin plastic tailored to their application for a low price. These headwinds have made plastic recycling processes slower to reach economic viability than recycling processes for metal, glass, and paper.
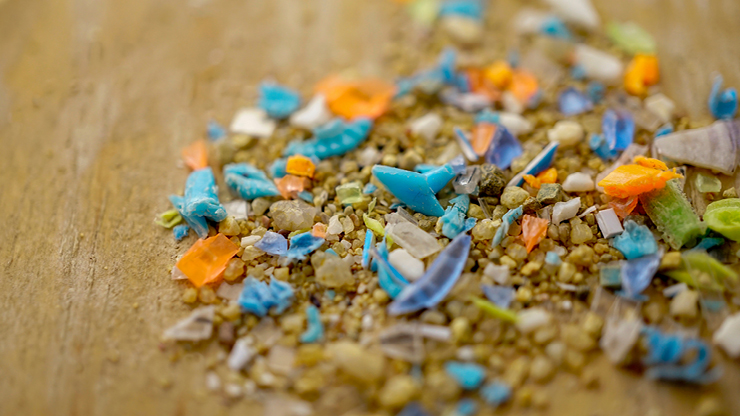
Safety and toxicity concerns
Many plastics emit harmful volatile organic compounds (VOCs) during the recycling process, and all plastics are toxic when burned. To recycle them safely, facilities must employ potentially expensive safety measures such as ventilation systems and respirators. For plastics like acrylonitrile butadiene styrene (ABS), polystyrene (PS), and polyvinyl chloride (PVC), VOCs and hydrogen chloride are obstacles to the recycling process.
If not properly cleaned or carefully processed, recycled polymers may also be contaminated by food residues, cleaning products, waste products, VOCs, or burnt plastic, limiting their applications. While recyclers can ensure food-safe plastic with careful testing and adherence to regulations, this often makes the recycling process more complicated and costly than the manufacturing of virgin plastic.
Release of microplastics
Although less problematic for growing methods like chemical recycling and dissolution recycling, mechanical recycling involves the shredding and processing of waste plastic. This can release microplastics into the plant’s wastewater.
Microplastics are any non-biodegradable plastics smaller than 5 millimeters. Microplastic waste is a concern to some because its size makes it difficult to effectively collect and recycle or dispose of, allowing it to build up in the environment. To address these concerns, many approaches to the filtration and disposal of microplastic waste are being developed.
In mechanical recycling, microplastic release is usually mitigated through filtration systems. Although filtration can’t remove all of the microplastics produced, mechanical recycling still reuses the waste for new products in the process. If the plastic was burned, placed in a landfill, or lost to the environment, far more pollutants would be released than if it were mechanically recycled and no raw materials would be recovered.
Reporting
The true extent of recycling and other processes used to dispose of plastic waste are unclear. If the plastic is exported for recycling, many governments report it as recycled with no way of confirming the outcome. As a result, many countries engage in the environmental dumping of plastic waste by exporting it to foreign entities that incinerate it or store it in landfills. Statistics may also cite the amount of plastic waste collected rather than the amount recycled, which fails to account for the weight of contaminants and the plastics collected that are not recycled.
Resin identification codes
Resin identification codes allow a consumer or recycler to determine the type of plastic used to manufacture a product. Although the codes were intended to be useful in recycling, not all countries require them and many of the types are not widely recycled. Resin identification codes are mostly useful to consumers who must separate their plastic waste by type before it enters the recycling collection system.
Plastic Identification Code | Type of Plastic Polymer | Common Applications | Percentage of All Plastic Waste (2019) | Frequency of Recycling |
![]() | Polyethylene terephthalate (PET) | Bottles, electronics, jars | 7% | Widely recycled |
![]() | High-density polyethylene (HDPE) | Large bottles, buckets, water and gas pipes, bags | 12.6% | Widely recycled |
![]() | Polyvinyl chloride (PVC) | Piping, packaging, cable insulation, stretch wrap | 6% | Usually not recycled |
![]() | Low-density polyethylene (LDPE) | Lids, flexible bottles, frozen food packaging, food-safe stretch wrap | 13.9% | Sometimes recycled |
![]() | Polypropylene (PP) | Disposable dishware, take-out containers, bottle caps, reusable dishware | 17.6% | Sometimes recycled |
![]() | Polystyrene (PS) | Foam food containers, packaging, disposable dishware | 4.3% | Rarely recycled |
![]() OR No Code | Other | Varies widely | 38.6% | Rarely recycled |
Advanced plastic sorting and technologies
Researchers, manufacturers, and governments are working towards a circular plastics economy by developing recycling processes that can be economically viable at scale for each major type of plastic. But to make these processes useful, waste plastic must be accurately sorted and recycled plastic must retain its quality.
Plastic recyclers circumvent inaccurate or missing resin codes with instruments that can rapidly identify plastic types with infrared scanning. Mechanical recycling processes use complex systems of tumblers, fans, and conveyors that accurately sort plastic by type, weight, and even color. Dissolution recycling can reduce the need for sorting and cleaning by allowing a single plastic type to be dissolved and separated from a bulk of mixed waste, ensuring its purity.
While accurate sorting and higher purity improve the quality of recycled material, the countless combinations of unknown additives in mechanically recycled plastic make its properties unpredictable. Recyclers and manufacturers restore the quality of recycled plastic using additives, which improve physical properties, increase processability, and prepare the material for new uses.
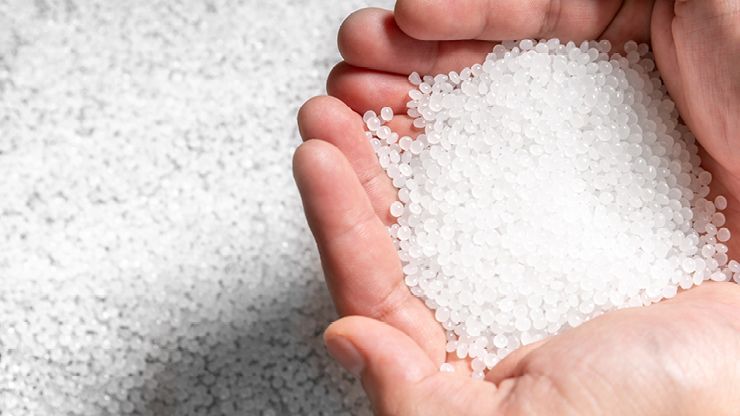
Closed-Loop vs. Open-Loop Recycling
Today, many recycling facilities use open-loop recycling. In these processes, manufacturers recycle one product into a different product. The new products often serve much different purposes than the old ones—for example, many open-loop recyclers turn PET bottles into fabrics, carpets, and plastic lumber. Because the quality and potential applications of the plastic decrease each time it’s recycled until it’s eventually unusable, these processes are also known as downcycling.
But theoretically, plastic can be mechanically recycled many more times than open-loop processes allow. Processes that achieve the repeatable remolding of plastic waste are examples of closed-loop recycling. In a closed-loop process, a used plastic product is endlessly recycled into the same new product, saving raw plastic, energy, and additives.
One company, for example, has developed an innovative closed loop. Their plant sorts HDPE bottles and PP bottle caps from municipal plastic waste, then recycles them into high-quality plastic that is then purchased by various companies for use in new bottles and bottle caps.
However, the quality of the recycled plastic is difficult to maintain in both approaches. In open loops, additives and other forms of reprocessing are often necessary to bolster the recycled plastic’s quality. In closed loops, imperfect mechanical recycling can also degrade the quality of the plastic over time. Recycled plastic may be contaminated by other waste or the recycling process, making it unsuitable for consumer goods without additional processing and quality control steps.
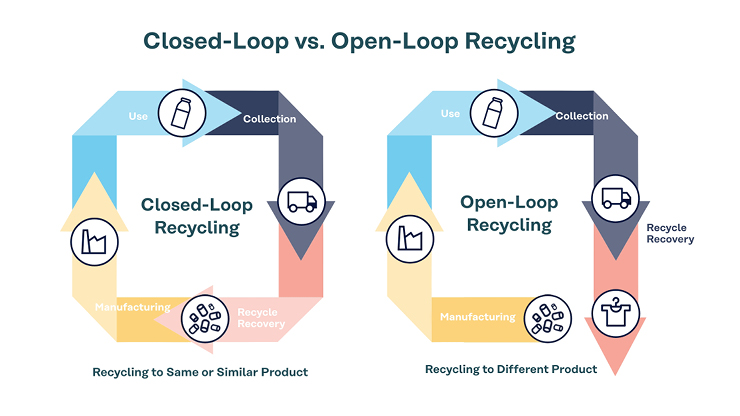
Kuraray’s contribution to plastic recycling
Even a perfect, closed-loop recycling process experiences a loss in plastic quality over time. That’s why many recycled plastics rely on additives to maintain their physical properties.
We supply SEPTON™ and HYBRAR™, thermoplastic elastomers that are highly compatible with polyolefins such as polyethylene and polypropylene. By adding these thermoplastic elastomers to the polyolefins, impact resistance can be improved. When recycling plastics, impact resistance may decrease. Thermoplastic elastomers can be used as impact modifiers to improve the properties.
Legal requirements
The EU and EFSA work to ensure the progress and safety of recycling in Europe through legislation. Currently, European plastics producers are in support of the European Commission’s proposal to set a mandatory 30% recycling target for plastic packaging.
In addition to the existing regulations and best manufacturing practices for food contact materials (FCMs), the EU established new restrictions in 2022 that outline safety requirements for recycled plastic FCMs and allow recycling processes to be approved for FCMs.
Is plastic recycling truly effective?
Plastic recycling began as a popular concept. As concerns about growing volumes of non-biodegradable waste, greenhouse gases, and environmental pollution mounted, the ability to remold plastic into new products seemed like the perfect solution.
To address concerns about non-biodegradable plastic pollution, the oil and plastic industries began campaigning in support of recycling. Companies and governments began organizing a system of plastic identification and collection—but the problem wasn’t solved.
As petroleum companies already knew, plastic recycling was a new technology that wasn’t yet commercially viable. Most plastics weren’t truly recyclable, and those that were had inferior qualities that limited their usability. For decades, “recyclable” plastic waste has been collected only to wind up in landfills or incinerators.
But plastic recycling, once only a new field of study, is quickly becoming a global area of interest. The world has realized that because plastic is here to stay, recycling is necessary—and advancements in technology and policy are steadily driving it toward economic viability.
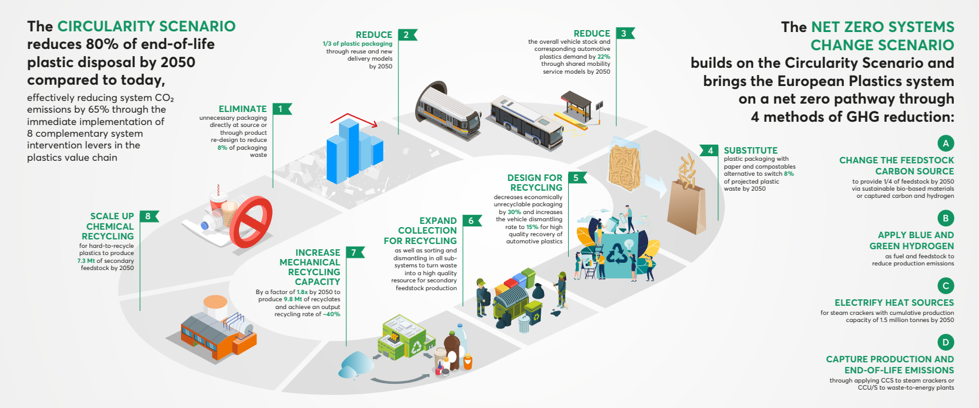
Although a truly circular economy for the plastics industry may be unrealistic, an increasingly circular recycling process driven by advances in technology and policy will benefit manufacturers, consumers, and the environment. A European plastics economy of 78% circularity could lead to an 80% reduction in plastic waste and a 65% reduction in carbon emissions by 2050 (SYSTEMIQ, 2022).
Plastic recycling may not have been effective at its inception—but today, it can be.
Conclusion
Plastic recycling is an evolving industry and a crucial component of waste management. Although challenges exist to a circular plastic economy, advances in processing and additives are rising to meet them.
Contact