Polymer modification
Polymer modification imparts desired properties to the resulting new material such as higher thermal stability, impact strength, stiffness, biodegradability, flexibility, etc.
It is often economically attractive to turn relatively inexpensive standard plastics into new materials with tailored properties through polymer modification. The choice of the appropriate additive depends on the polymer in question, the desired effect and the processing conditions.
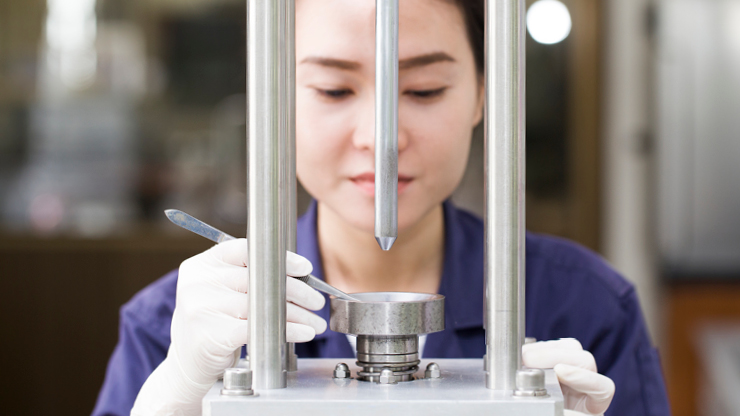
Types of polymer modification
What you should know: Polymer modifications can be divided into two general categories – physical modifications in various forms, and chemical modifications, in which the polymer is chemically altered to form a new material.
Physical modifications
Physical modification includes processes like entanglement, entrapment as well as radiation-induced modification.
Chemical modifications
Chemical modification is a common alternative for synthesizing new polymers. Well-known examples are vulcanization and solvent-free reactive extrusion.
Surface modification vs. bulk modification
Surface properties are critical for the materials to function as they’re intended. Polymers on their own often do not have the required surface properties. Thus, surface modification techniques have become important especially for the plastics industry to obtain the desired properties like abrasion resistance and water repellency.
Another form of polymer modification is bulk modification using reactive or non-reactive extrusion. Examples of the bulk modifications are shown below.
Polymer blends and alloys
Another common way to modify polymers is to blend them with other polymers or modifiers by extrusion. The mixed polymers are often referred to as alloys. This relatively simple method can be used to refine commercially available polymers such as PE, PS or PP into customized materials with higher added value.
Crosslinking, branching, chain scissoring
Polymers can be modified using other processes such as crosslinking, branching and chain scissoring. Crosslinking with the aid of the electron beam process is normally used for molded parts to turn a thermoplastic into a thermoset. Branching is performed on granules to change their melting properties. Chain scissoring, on the other hand, breaks the bonds between molecules to obtain specific particle sizes.
Polymers to modify
It is impossible to present a complete list of all modifiable polymers in one article since the possibilities are nearly endless. Kuraray’s elastomers can be used as a modifier for various kinds of plastics. In the following paragraphs, let us take a closer look at some plastics commonly modified with Kuraray’s polymers.
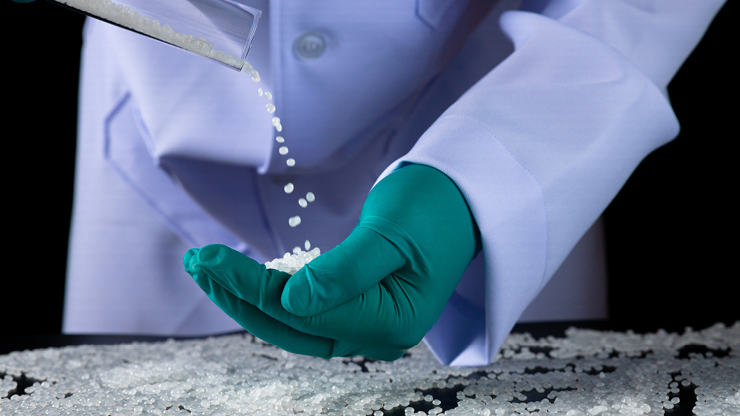
Polypropylene (PP)
Polypropylene (PP) is rigid with good heat resistance. However, the disadvantage of this plastic is its poor impact resistance, especially at low temperatures. Appropriate additives are used to improve the impact resistance and other properties of PP, such as transparency, weather resistance or flowability. For instance, HYBRAR™ 7311F and 7125F are added to PP in order to improve flexibility and transparency. These are especially suitable for applications such as medical tubes and medical bags. Also, SEPTON™ 2004F can help PP by improving its impact strength at low temperatures.
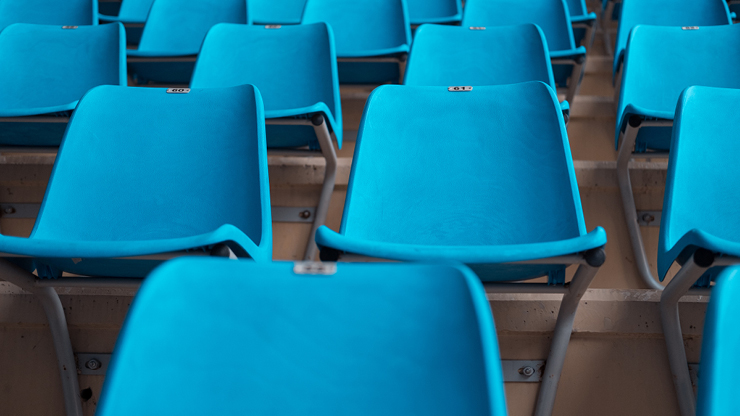
Read more:
Demonstrating polypropylene brittleness in the cold (ChemEd X)
Polyethylene (PE)
Polyethylene (PE) is a commonly used thermoplastic for a variety of applications. Advantages of PE include cost efficiency and cold temperature resistance. However, disadvantages such as heat resistance, stress cracking, poor bonding and poor weatherability often limit its uses. Polymer modification with SEPTON™ 4000-series and 8000-series often remedies these weaknesses.
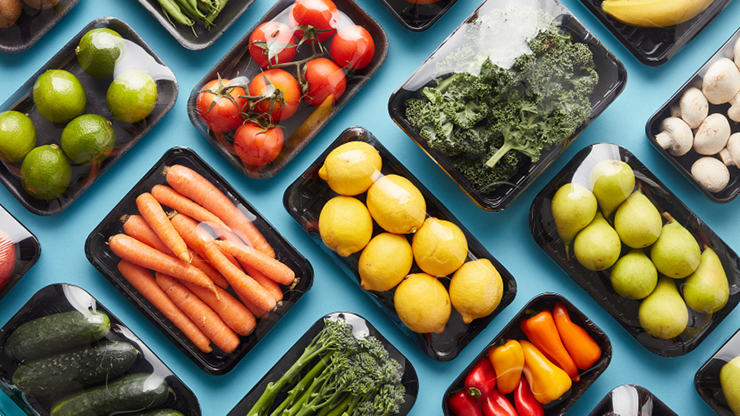
Polystyrene (PS)
Polystyrene (PS) is a transparent plastic characterized by high rigidity, resistance to breakage and a high surface quality. A well-known product of foamed type polystyrene is STYROFOAM™.* Adverse properties of PS can be improved by polymer modification. SEPTON™ 2104 and 8006 can be used with PS to improve impact resistance.
*STYROFOAM™ is a registered trademark of Dow Chemical Company
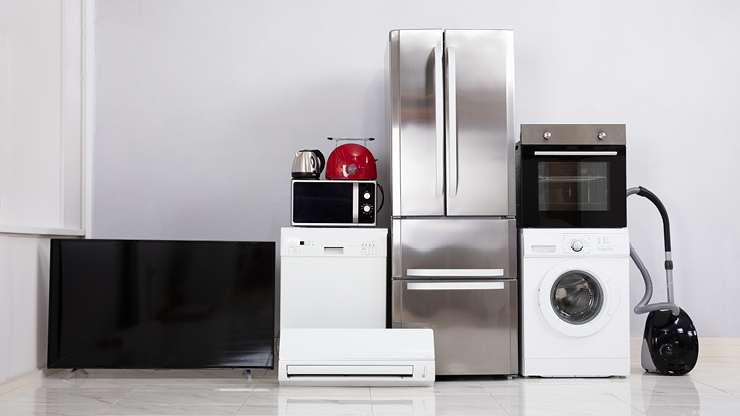
Polyvinyl chloride (PVC)
Polyvinyl chloride (PVC) is the third most important polymer for plastics after PE and PP. Without the use of polymer modification, PVC has limited physical properties. Modifications range from physical blending to chemical reactions that alter the chain structure of PVC.
Polycarbonate (PC)
Polycarbonate (PC) is a fairly tough material. However, thicker parts of the plastic can become brittle due to lower notch impact strength. This problem can be countered by adding a suitable polymer that significantly increases the notch impact strength. SEPTON™ can help improve PC’s impact strength while maintaining processability.
Acrylonitrile butadiene styrene (ABS)
Who does not know the popular LEGO® bricks? They are a well-known application of the plastic “acrylonitrile butadiene styrene (ABS)”. ABS is characterized by a number of positive properties including excellent impact resistance, high heat resistance and high surface gloss. Furthermore, this plastic is easy to process.
Disadvantages are its medium to weak flexural strength and poor weathering resistance. In order to improve the weaker mechanical and physical properties of ABS plastic, it must be modified. SEPTON™ and HYBRAR™ can be used as an ABS modifier adding impact strength, flexibility, elongation and more. Additionally, HYBRAR™ 5127 and 7125F can improve damping properties at various temperatures.
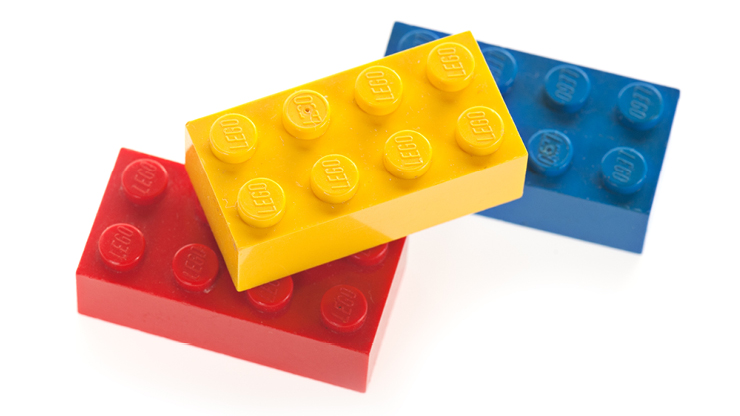
Polylactide (PLA)
Polylactic acid (PLA) is a biodegradable and bio-based material that can be used as a substitute for low-cost petroleum-based polymers. PLA is easy to process and it exhibits good thermoplasticity. Its shortcomings include brittleness and low toughness which limits the application of PLA due to plastic deformation. To improve the performance of PLA, SEPTON™ BIO-series is often used to make it softer and more durable.
Polyphenylene Ether (PPE)
Polyphenylene ether (PPE) is a high-temperature-resistant, high-performance thermoplastic. PPE blends are used for molded parts in multiple markets including electronics, household, automotive, and medical technology. The properties of PPE can be modified over a wide range by blending with modifiers like SEPTON™ for added impact resistance.
Thermoplastic Polyester Elastomer (TPE-E aka. COPE aka. TPC)
You may know thermoplastic polyester elastomer (TPE-E) by another name? TPE-E is also known as COPE or TPC. The plastic has very good resistance to heat aging and chemicals and its low-temperature impact strength is excellent. However, TPE-E only has a limited hardness. This disadvantage can be overcome by modification with appropriate additives.
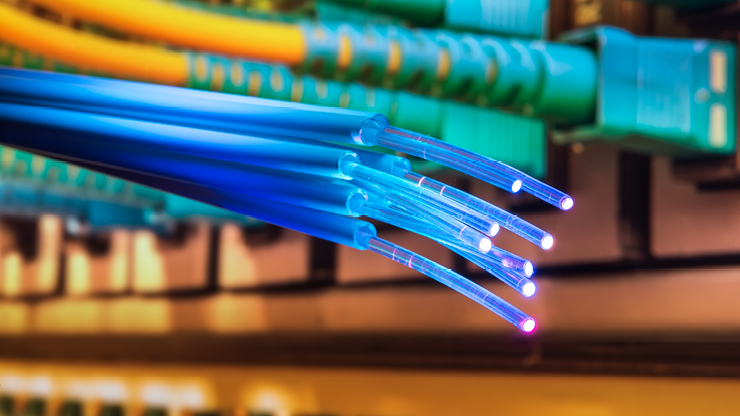
Polyamides (PA)
Polyamides (PA) best-known application is nylon. Depending on the requirements, the material properties of polyamides can be optimized by modifying the material to improve toughness and weather resistance.
Polybutylene terephthalate (PBT)
Did you know that polybutylene terephthalate (PBT) has properties and composition similar to PET? Important advantages of PBT are its resistance to solvents combined with limited shrinkage during forming. Its stiffness, strength and glass transition temperature are lower than those of PET and its resistance to hydrocarbons and acids are unsatisfactory. Polymer modification can help to reduce these limitations. For instance, SEPTON™ can improve the impact resistance of PBT at various temperatures.
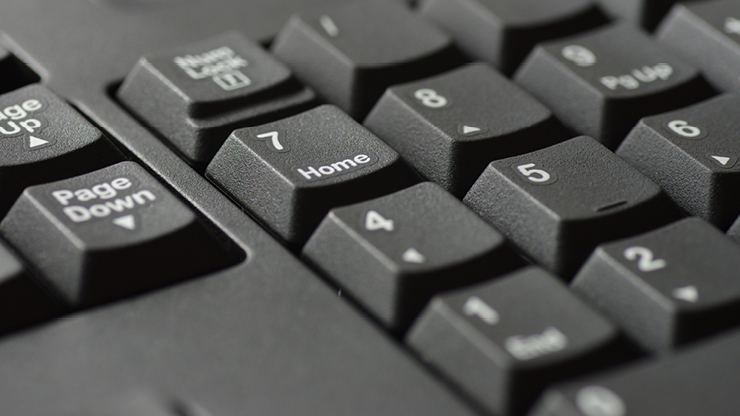
Ethylene vinyl acetate (EVA)
Ethylene vinyl acetate (EVA) containspositive properties like heat resistance and aging. The elastic, colorless plastic is commonly used in shoe soles and floor coverings. Furthermore, solar cells in photovoltaics use EVA Properties of EVA such as thermal stability, transmittance or volume resistance can be increased with the aid of polymer modifications.
Polyethylene terephthalate (PET)
Polyethylene terephthalate (PET) should be mentioned. This thermoplastic is often used with plastic bottles. Modifications are used with PET to make it easier to process, to prevent microbial contamination, and to improve clarity, strength, transparency and durability. Surface modification area used with PET.
Benefits of polymer modification
Polymer modification is intended to impart various desired properties to the modified material. Polymer modification can improve important properties of plastics including compatibilization, toughness, heat resistance, weathering resistance and impact resistance.
Compatibilization
By mixing polymers, new materials can be developed that combine the properties of several polymers. However, due to different chemical structures, most polymers cannot be mixed with each other. A multiphase morphology of the blends is the result. In such cases, compatibilizers help to improve the morphology of plastic compounds.
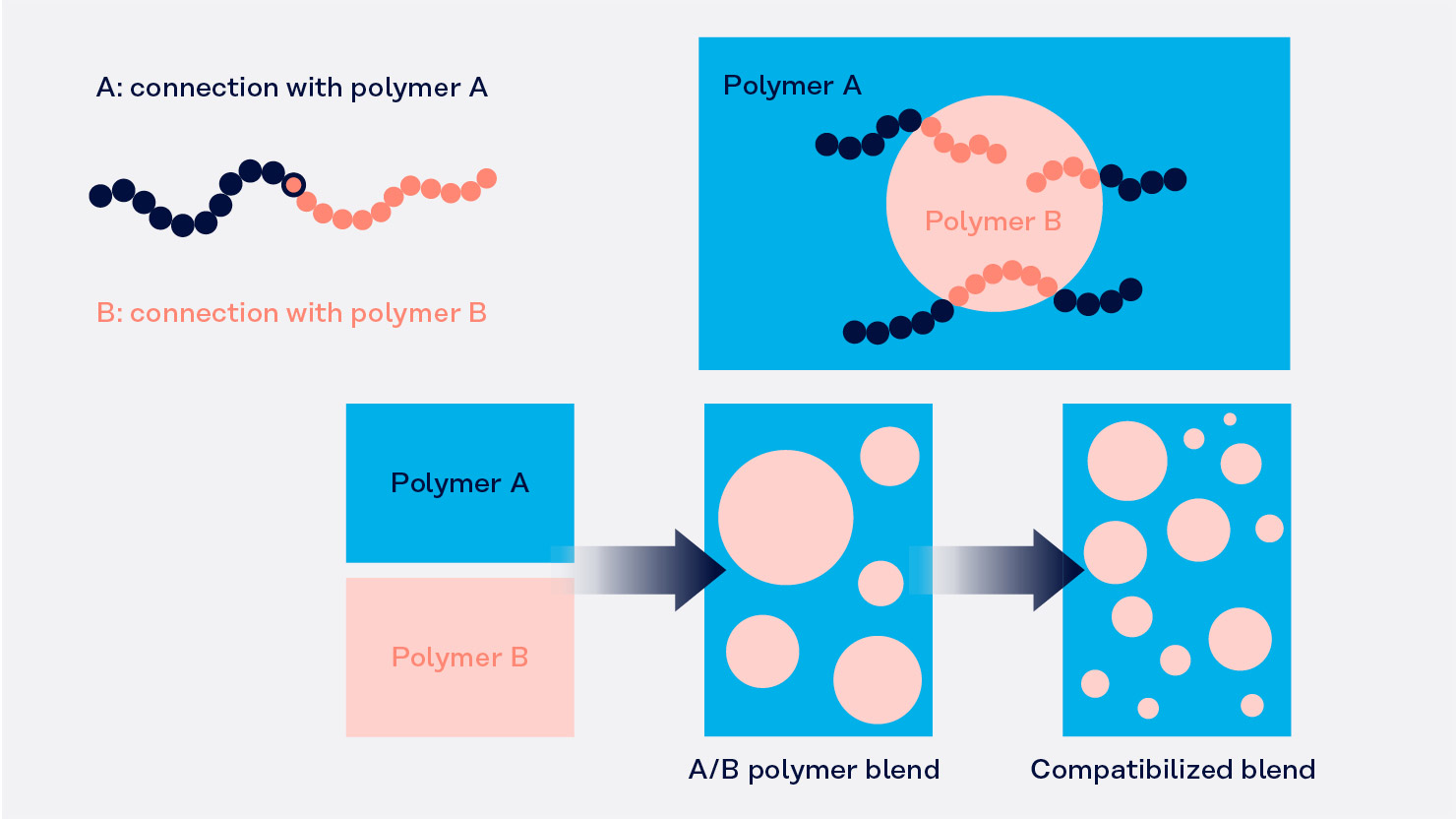
Toughness
Improving toughness is about strengthening the impact resistance of previously brittle materials. In the development of polymers from several components, the toughness of elastomers dispersed in relatively brittle plastics can have a positive impact.
Heat resistance
Heat resistant polymers play a key role in many fields such as electronics, automotive, aerospace, and more. In processes such as insert molding where composites are made from resins and metal parts, the resins must have good heat shock resistance to prevent fatigue fractures. Flame retardant modification, can produce materials with application-optimized properties such as high heat resistance.

Weather resistance
Most polymers undergo irreversible physical and chemical changes outdoors due to UV radiation, air, heat and moisture. The properties altered by weathering can include discoloration or color change, loss of gloss, surface erosion and other consequences. Modification of polymers can overcome these weaknesses or prevent the change. Examples are the use of UV-absorbing agents or antioxidants.
Impact resistance
Plastics are often used in very demanding applications. These applications include damping or vibration damping. By combining different polymer types, plastics can meet the very specific requirements. The use of appropriate modifiers such as compatibilizers makes a decisive contribution to this.
Flowability
Flowabilty is the capacity to move by flow that characterizes fluids and loose particulate solids, which especially matters when you are considering injection molding. With low flowability, the flow distance of materials on the mold will be shorter which affects productivity.
Our materials for polymer modification
SEPTON™
The high-performance TPE SEPTON™ is used in a number of TPE compounds and can be processed in a wide variety of forms. Specific grades are certified and used in consumer goods, medical, mobility and oil modification applications. Hydrogenation ensures excellent heat and weather resistance.
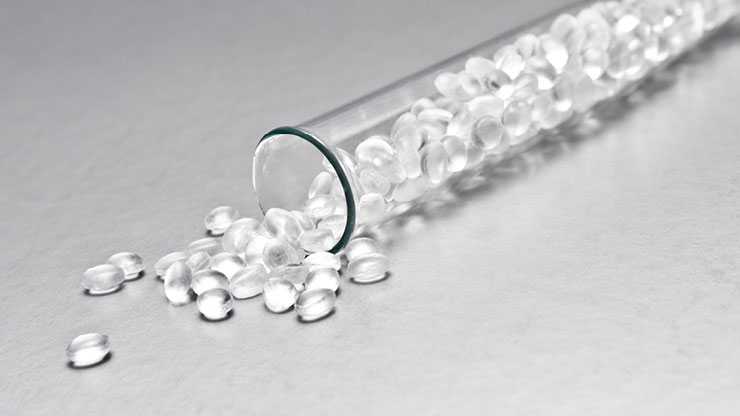
SEPTON™ BIO-series
Bio-based TPE SEPTON™ BIO-series is a unique hydrogenated styrene farnesene block copolymer (HSFC). Using SEPTON™ BIO-series enables compounders to produce compounds with high bio-based content. Common applications include adhesives, sealants, compounds, coatings, and polymer modification.
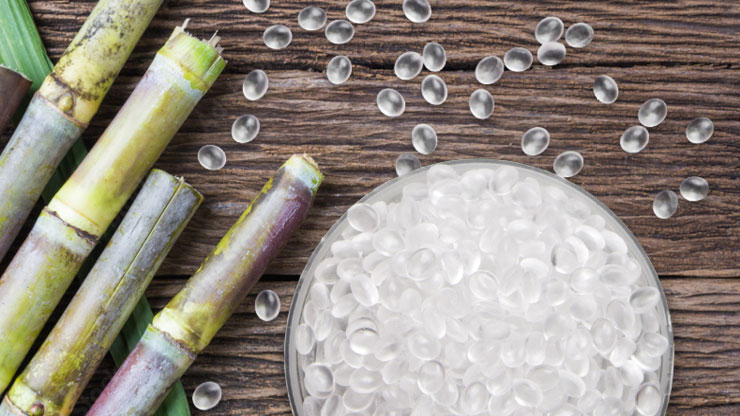
HYBRAR™
HYBRAR™ is a vinyl-rich, high-performance TPE with high vibration damping properties. Hydrogenated grades of HYBRAR™ have excellent weatherability and compatibility with polypropylene resulting in excellent transparency and clarity when blended. Comon applications include medican films and tubing as well as molded components which are used in damping applications. The non-hydrogenated grades are used in vibration damping sealants.
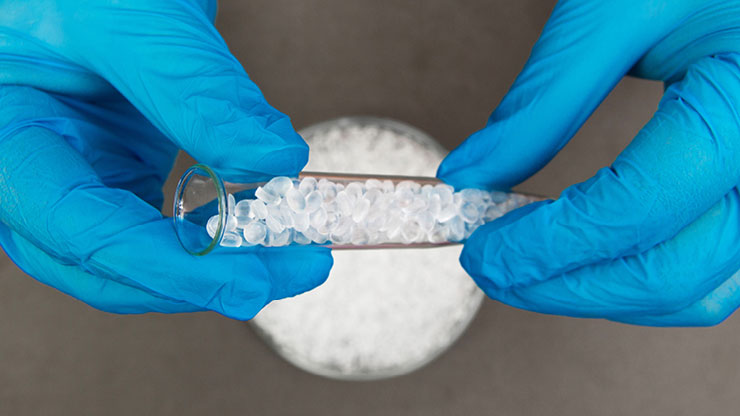
Contact for business
Do you have any questions? We will be happy to help you! Please contact us to learn more about Kuraray materials for polymer modification.
Contact