Elastomers in 3D printing
3D printing technology originated in the 1980s. Initially used for rapid prototyping, this additive manufacturing technology has developed very fast. Today, companies are increasingly using 3D printing to produce functional components for end users. In the near future, it will even be possible to use 3D printers to manufacture customer-specific products on an industrial scale.
As well as offering unique manufacturing benefits, 3D printing is a sustainable production process because it minimizes waste. Unlike subtractive manufacturing, additive manufacturing (3D printing) uses only the amount of material that is necessary. Moreover, plastics waste can be recycled and used to manufacture new products.
For applications requiring rubber-like properties, the manufacturing industry often uses thermoplastic elastomers (TPEs) for 3D printing. Recently, TPEs have also been used in additive manufacturing as an addition to main printing materials (like PLA and ABS). TPEs can be used to make consumer goods, sports equipment and electronics as well as components for the automotive and construction industries. TPEs are suitable for use as 3D printing elastomers in the filament deposition modeling (FDM) process, Pellet Additive Manufacturing (PAM) and as powder in the selective laser sintering (SLS) process. Thermoplastic polyurethane (TPU) is a subcategory of TPE. Like other TPEs, it can preferably be processed in filament or granulate form.
TPEs are ideal for applications requiring flexibility, durability and resistance. 3D printing with TPEs is less expensive compared to other materials, e.g. silicone printing, and more suitable for large-scale industrial applications. TPEs can be used for both prototyping and the manufacture of components for end users. Products from Kuraray are particularly suited for the further processing of PLA, acrylonitrile butadiene styrene (ABS) and polycarbonate (PC).
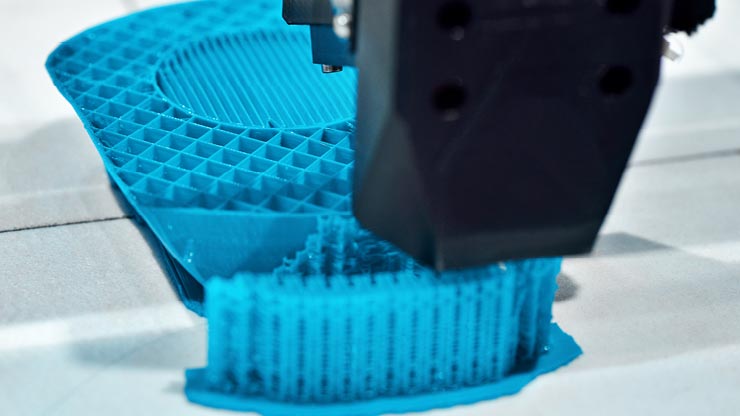
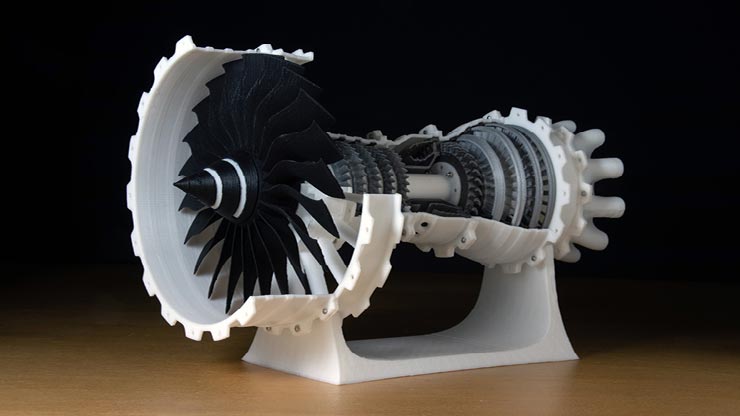
Types of 3D printing
3D printing refers to various additive manufacturing technologies where objects are built up layer by layer. Various materials are used in these processes, including metal, sand, paper and, most frequently, plastics. The three most common methods in relation to 3D printing elastomers are FDM/PAM, SLA and SLS printing. The difference is the format of the materials fed to the machine (liquid, molten or powder).
Filament (FDM) and pellet printing (PAM) are extrusion processes where the 3D printing elastomers are melted to produce the prototyped end-product. Stereolithographic (SLA) printing is a vat photopolymerization process, where a liquid or resin is deposited in layers to build up an object. Selective laser sintering (SLS printing) is a powder bed fusion technology where a powder is added to produce an object.
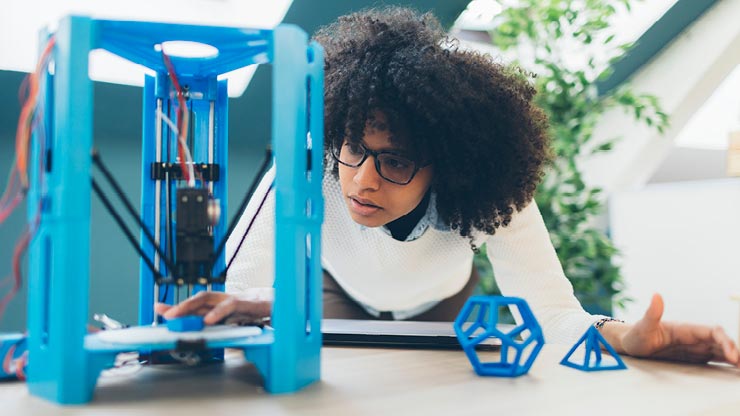
Kuraray’s product range for 3D printing
Kuraray’s product range includes industry- and customer-specific TPEs for additive manufacturing. These materials deliver reliable results, even in challenging production conditions. Kuraray’s 3D printing elastomers have excellent elasticity, damping properties, transparency and flowability, plus improved resin elasticity. Selected materials can also be used as modifiers for bio-based polymers such as PLA. The 3D printing elastomer solutions of Kuraray come with advantages as well as challenges regarding the printing process.
Features and benefits
- Soft, flexible material
- Improves the impact resistance and flowability of PLA, ABS and PC
- High clarity
- Longer service life
- Good impact resistance
- Improved flowability and efficiency
- Soft-touch surface properties
Limitations
Due to inherent physical, thermal and mechanical properties of 3D printing elastomers, the additive manufacturing process remains challenging.
Points to consider when selecting the most suitable 3D printing technology
Key criteria that need to be considered when selecting the most suitable technology for processing 3D printing elastomers are budget, mechanical requirements, feeding of the system, geometry of the parts, and appearance.
3D printing may be the ideal solution for small batches. By contrast, other manufacturing processes may be better suited to large-scale production. For components with complex, functional geometries, 3D printing is often the only option.
To select the most suitable process, the benefits and limitations of the various technologies need to be considered in the light of the key product specifications. Below, there is a detailed overview of the most common 3D printing processes for elastomers.
Filament printing
Fused deposition modeling (FDM) is a desktop 3D printing technology widely used to produce plastic parts. In this filament printing process, the 3D printing elastomers are extruded and deposited, layer by layer, on the build platform. FDM is suitable for rapid prototyping, inexpensive modeling and applications where high precision and surface quality are not essential.
FDM is the most cost-effective 3D printing method for the manufacture of customer-specific thermoplastic parts and prototypes. The high availability of this technology reduces lead and delivery times. A wide range of thermoplastic materials is available for prototyping and non-commercial functional applications. However, FDM is less suitable for complex parts because resolution and precision are lower than in other additive manufacturing technologies. Moreover, objects produced with this technology may have visible surface structures and therefore require post-processing.
In general, the more flexible the elastomer resin, the slower and more difficult the feeding of the filament printing process.
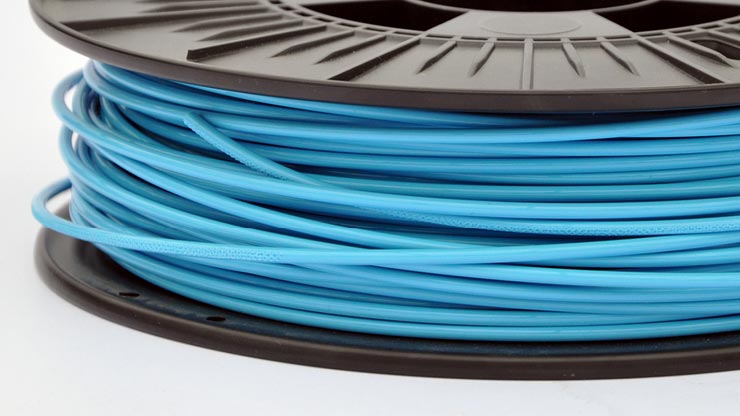
How the FDM process works:
- A spool of 3D printer elastomers is placed in the printer. This elastomer filament is heated within the extrusion head to the desired temperature, then fed to the extruder head and nozzle, where it melts.
- The extruder head is fixed to a triple-axis system. The molten material is extruded into thin filament strands which are deposited in predefined layers on a surface, where they cool and solidify. Cooling can be accelerated by a blower in the extruder head.
- Once one layer is complete, the next layer is applied. The process is repeated until the part is complete.
Pellet printing
The difference between filament printing and pellet printing is the type of extrusion process. In filament printing, an elastomer base is fed via a gear. This applies pressure to press the 3D printing elastomers through a heater block, where it melts so that it can be extruded through a nozzle. In pellet extruders, pellets are fed through a hopper into a cylinder with several heating zones. A motor-driven screw mechanism drives the pellets through the cylinder to the extruder nozzle.
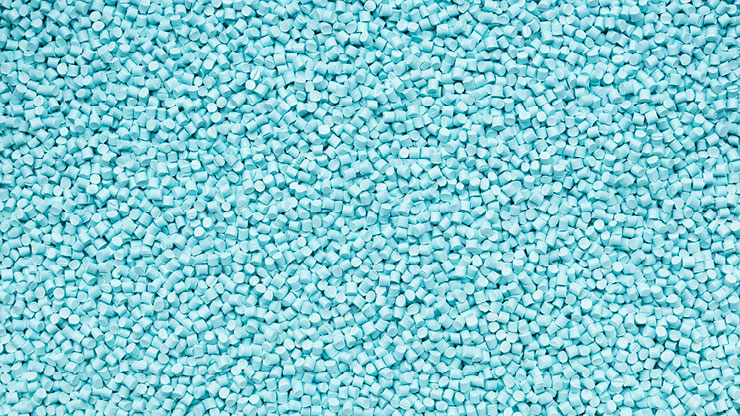
Features and benefits
- Higher throughput/deposition rate
- Far greater choice of materials, especially very soft materials
- Pellets have an improved price-performance ratio compared to regular filaments
- Larger parts can be produced
SLA printing
Stereolithography (SLA printing) is a common industrial process for 3D printing elastomers. Its principal features are accurate details, smooth surfaces, narrow tolerance ranges and good mechanical properties such as weather resistance, isotropy and flexibility. The finished objects have a high-quality surface structure.
This process is widely used in the medical/dental sector, for example, to produce anatomical models. It is also used to produce castings for mass production, e.g., for toys and jewelry.
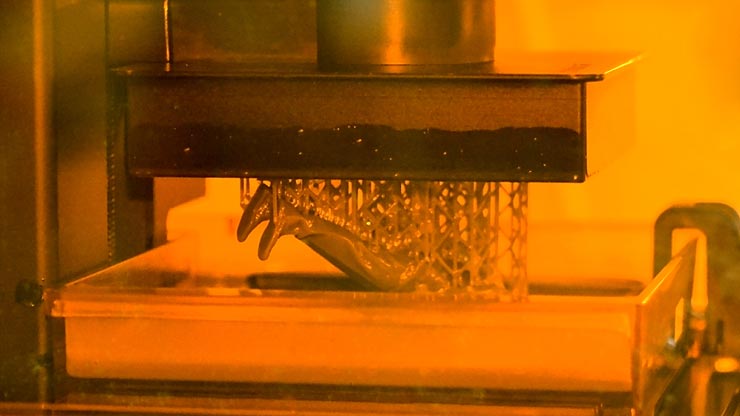
Features and benefits
- Production of high-precision objects with complex details
- Very smooth surface (ideal for visual prototypes)
- Special SLA materials are available (e.g., clear, flexible and pourable resins)
Limitations
- The objects are generally brittle, so they are not as suitable for functioning prototypes as other 3D printing techniques
- The appearance and mechanical properties of the objects deteriorate over time if they are exposed to sunlight
- Support structures are required
- Post-processing is necessary
How the SLA printing works:
A typical desktop SLA printer contains a UV laser to cure each layer of the component created from a vat containing a light-sensitive resin. Wherever the UV laser hits the resin, the liquid cures.
Each laser pass creates a very thin layer of the object, which is bonded to the previous layer (or to the build platform) and the base of the vat. The build platform is then lowered by the thickness of the layer, until the production process is complete.
SLS printing
Compared to SLA printing, Selective Laser Sintering (SLS) printing is still in development to overcome its technological limitations regarding 3D printing elastomers. Even if SLS printing is a common technology in the industry, today’s procedures tend to clump TPE base powders. But in the near future, SLS processing that meets the highquality standards of manufacturers will also be available for 3D printing elastomers.
Features and benefits
- Production of functional parts and prototypes requiring good mechanical properties
- The printing process requires no support structure, which allows manufacturers to design complex objects
- High mechanical stability
- High price-performance ratio, even for small and medium batches
Limitations
- SLS printing requires post processing and finishing due to a powdery surface and internal porosity
- Depending on the size and thickness of an object, oversintering can lead to the loss of small details or holes
- Due to the sintering process, shrinkage and warping are more likely to occur depending on the object’s geometry
How SLS printing works:
A powder is heated below the melting point of the 3D printing elastomers. The laser scans a cross-section of the 3D model and heats the powder at the melting point of the material so that the powder fuses together to a solid object. Then, the platform moves downwards into the build chamber by one layer and the new layer gets sintered analogously. This repeats until the last layer is fused together. Up until then, the unfused powder supports the printed object, which is why no additional support structure is needed. Afterwards, the object cools down in the build chamber.
3D Printing – Opportunities with KURARAY LIQUID RUBBER
UV-curable grades of KURARAY LIQUID RUBBER, UC-102M and UC-203M can used for very soft prints or as modifiers for acrylic or urethane-based photo resins to improve the impact resistance of the finished parts.
These UV-curable grades have excellent performance, especially:
- Good low temperature properties (low Tg)
- Low shrinkage ratio
- Good moisture absorption and permeability resistance
- Sufficient insulating properties
- Sufficient adhesive properties
Contact